↧
Motor Nameplate Revealed
↧
The Gas Turbine
THE GAS TURBINE
The gas turbine comes under the heading of high speed rotating machinery (i.e., Dynamic versus reciprocating operation and in excess of 3000 R.P.M.).
Gas turbines must operate at high speeds for proper efficiency and economy. While speed is essential in gas turbine operation, it is also a danger to the machinery. In the event of trouble the high speed limits the amount of time available to safely shut the machine down. Human reaction time, from receipt of information to starting action is normally in excess of one second. Human reaction is not able to start the shutdown of a unit within a time frame necessary to prevent major damage.
Let us look more closely at this speed problem by comparing a reciprocating engine’s speed versus a gas turbine’s speed. A typical recip engine that does 900 R.P.M. ( or 15 revolutions a second) is 15 times slower than a typical gas turbine doing 13,500 R.P.M. ( or 225 revolutions a second). Now you have 1/15 of the time necessary to react to a problem occurring. Because of this speed-time problem high speed machinery controls are highly automated, particularly with regard to the safety systems.
Another factor of concern with high speed rotating machinery is the problem of vibration and its effects on the machinery. The faster the speed of a machine, the more critical it is to have the rotating elements balanced properly, also the less vibration the machine can take without
Image may be NSFW.
Clik here to view.
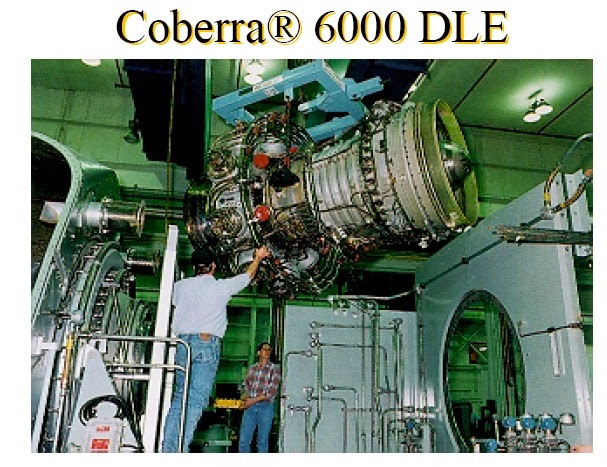
damage. The limits of allowable vibration in a high speed machine are much less than in a low speed machine. The high speed has also caused manufacturers to consider natural frequencies, criticals, and torsional criticals versus rotational speeds as a problem area.
While the gas turbine has some drawbacks; it is still a very efficient, economical, and reliable piece of machinery. All of the work done in gas turbines is done dynamically in a continuous process, without valves or a split cycle,( i.e. recip. Engine intake, compression, power exhaust).
Because of this continuous process, the gas turbine gets a maximum horsepower per unit weight much greater than the reciprocating engine.
Dry Low Emission variant of RB211
The design of gas turbines is to use the fluid molecules as the only contact in or rubbing parts in
the machine. The gases flowing through the machine and the oil in the bearings are the only contacting mediums with the metal parts of the machine.
This design creates a high degree of mechanical reliability in theat mechanical wear is severely curtailed.
Having now characterized the equipment, let us consider how it works and how it is similar to what you are familiar with. I am sure you have all heard of a turbocharged automobile engine.
In this system air is compressed by the compressor of the turbocharger for delivery to the cylinders. After using the air in the combustion process, the exhaust gas is ducted to the turbine section of the turbocharger. By replacing the recip engine with a fire box, where continuous burning takes place, we turn the system into a gas turbine.
DLE Variation of the RB211 Gas Turbine
Now we have an engine which compresses air by dynamic mechanical energy. The compressed air enters the combuster where fuel is added and burned, thus increasing the energy level of the combustion products above that of compressed air only. The hot gases expand through the turbine where some of the hot gas energy is converted to mechanical work. If the design is reasonable, the mechanical work produced by the turbine will be great enough to drive the air compressor and leave a surplus of energy available at the shaft to drive some kind of load such as a gas compressor or an electric generator.
In some cases, the exhaust gases are run through a heat exchanger and used to drive other machinery, also to heat liquids or gases for certain processes.
Image may be NSFW.
Clik here to view.
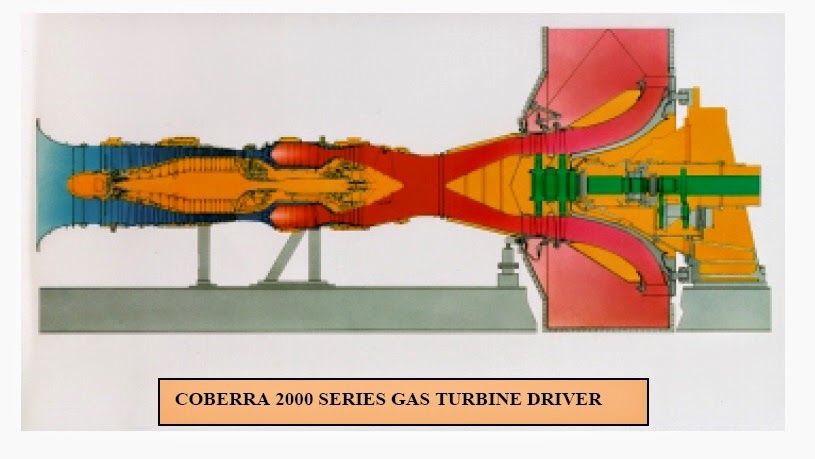
The idea to remember is the gas turbine can be broken into components to make it easier to understand.
CoCmobmubsutosrtor
GG Turbine
Gas Generator Anatomy
Non-DLE arrangement
VIGVs IP Compressor Bearings HP Compressor
Combustor GG Turbine
COBERRA 2000 SERIES GAS TURBINE DRIVER
↧
↧
Medium voltage power vacuum circuit breaker
Medium voltage power vacuum circuit breaker. (a) Side view showing vacuum bottles and(b) back view showing primary disconnect fingers.
↧
High Voltage Cables
↧
Low-voltage draw-out power circuit breaker
Low-voltage draw-out power circuit breaker.
(a) Front view showing name plate of CH-DSLII
and protective trip devices, (b) side view showing operating mechanism, and
and protective trip devices, (b) side view showing operating mechanism, and
(c) back view showing disconnect stubs and fi nger cluster, and CLF fuses.
↧
↧
Power Circuit For A motor
↧
500KV autotransformer
Type : Single-phase, outdoor
Altitude: ≤ 1000 m above sea level
Average ambient temperature : 30
Maximum Ambient temperature: 40
Cooling: Non inhibited mineral oil
(Nynas Libra or Shell
Diala D or equivalent)
Cooling class : OFAF
Rated power : 340 MVA
Voltage vector group : YN, a0
Insulation: Not uniform
Neutral grounding: solidly earthed
Rated voltages:
HV1 winding : 231 kV (400/√3 kV)
HV2 winding : 289 kV (500/√3 kV)
HV1 (400 kV) winding rated insulation level:
Highest voltage for equipment : Um = 420 kV
Switching impulse withstand voltage : consequence of HV2
Lightning impulse withstand voltage : 1300 kV
Power frequency withstand voltage: 140 kV
HV2 (500 kV) winding rated insulation level:
Highest voltage for equipment : Um = 550 kV
Lightning impulse withstand voltage : 1425 kV
Switching impulse withstand voltage : 1175 kV
Power frequency withstand voltage : 140 kV
Neutral terminal rated insulation level:
Highest voltage for equipment : 72.5 kV
Power frequency withstand voltage : 140 kV
Short circuit impedance
at 75 and rated voltage (400/500kV): 12%
Temperature-rise limits at rated power:
for windings : 65
for oil: 60
On-load tap-changer : “Vacutap” MR, Germany
tapping range : + 12 %
number of steps : + 15 x 0,8%
Sound pressure level: < 70 dB (A)
↧
3.6/6kv-26/35kv Three Core XLPE Insulated,steel wire armoured power cable.
↧
Welding of optical fibers.: Cables and cutting, optical instrument, couplings, crosses, connectors and adapters
The fibersare loaded inthe welding machine
Hello readers ! Everyone has heard about the optical fibers and cables. No need to tell where and for what uses optics. Many of you will encounter it at work, someone develops the transmission network, someone who works with optical multiplexers. However, I have not met the story about the optical cables, couplings, crosses, about the technology itself, and splicing cables. I - fitter of optical fibers, and in this (his first) post would like to tell and show you how it all happens, and often in his story will be distracted by other things related to this. I will rely mainly on their experience, so I fully admit that someone will say "this is not quite right,""here uncanonical."
Stuff happened a lot, so it was necessary to split the topic into parts.
In this first part you will read about the device and cutting a cable, about an optical instrument, about the preparation of fibers for welding. In other parts, if the topic would be interesting to you, I will discuss the methods and will show on video the process of splicing optical fibers themselves, about the basics and some of the nuances of measurements on optics, touch on welding machines and OTDR and other measuring instruments, show jobs fitter ( roofs, basements, attics, hatches and other field offices), tell a little about the fastener cables, wiring diagrams about, about the placement of equipment in telecommunication racks and boxes. It is certainly useful to those who are going to become fitter.
Network Technology *IT Infrastructure *
The fibers are loaded in the welding machine
Hello readers Habra! Everyone has heard about the optical fibers and cables. No need to tell where and for what uses optics. Many of you will encounter it at work, someone develops the transmission network, someone who works with optical multiplexers. However, I have not met the story about the optical cables, couplings, crosses, about the technology itself, and splicing cables. I - fitter of optical fibers, and in this (his first) post would like to tell and show you how it all happens, and often in his story will be distracted by other things related to this. I will rely mainly on their experience, so I fully admit that someone will say "this is not quite right,""here uncanonical."
Stuff happened a lot, so it was necessary to split the topic into parts.
In this first part you will read about the device and cutting a cable, about an optical instrument, about the preparation of fibers for welding. In other parts, if the topic would be interesting to you, I will discuss the methods and will show on video the process of splicing optical fibers themselves, about the basics and some of the nuances of measurements on optics, touch on welding machines and OTDR and other measuring instruments, show jobs fitter ( roofs, basements, attics, hatches and other field offices), tell a little about the fastener cables, wiring diagrams about, about the placement of equipment in telecommunication racks and boxes. It is certainly useful to those who are going to become fitter. All this I arch a lot of pictures (I apologize in advance for the paint-quality) and photos. Beware, a lot of pictures and text.
Entry
To begin with a few words about me and my work.
I work fitter optics. He started with a telephone operator and installer, and then worked in the emergency team in serving the main optics. Now I work in an organization that takes the general contractor for the construction of communication lines among different companies. A typical construction project - cable line connecting several containers of base stations GSM. Or, for example, several rings FTTB. Or something smaller - such as cabling between the two server on different floors of the building and the splicing at the ends of the cable crossover.
If the tender is won, looking for a suitable sub-contractors performing work (design and survey and construction). In some regions, it is our subsidiaries, some have their own equipment and resources, some hired an independent company. On our own shoulders rests mainly control, elimination of stocks of various subcontractors and force majeure, every agreement with landowners and administrations, sometimes drawing up the executive documentation and other constructed facilities. Often the need to work with optics: cook or digest somewhere optical coupling or cross, eliminate the effects of street racing knocked supports or fallen tree on the cable, hold the input control cable drum, to remove the trace section and so on. These are tasks I perform. Oh, and incidentally, when there is no problems in optics - other tasks from loading and installation via Express-haul to copying paper work. smile.gif
Optical cable, its types and entrails
So what is a fiber optic cable? The cables are different.
At the point of use - for exterior and interior linings (last rare and typically in data centers high-end, where everything has to be perfectly correct and beautiful). Under the terms of the gasket - Suspension (with Kevlar or cable) to ground (armor of iron wires), for installation in cable ducts (with corrugated metal armor), underwater (complex sverhzaschischayuschaya sandwich construction), for hanging on electric poles (except for the transfer of information vyponyayut role of lightning protection cable). In my experience, the most frequent suspension cables on poles (with Kevlar) and for laying the ground (with armor). Seldom come across a rope and gofrobronёy. More common cable that is essentially a thin coaxial optical patch cord (yellow envelope in singlemode and orange - in multimode, and one bit of Kevlar fiber, the two shells are paired). Other optical cables (without protection, underwater, for installation in the premises) - exotic. Almost all of the cables, with whom I work, have a structure like the one below.
1 - central strength member (in other words - from fiberglass rod, although it may be wire in polyethylene covering). Used for centering tube modules, giving rigidity around the cable. For it is also often fixed cable coupling / cross-country, clamping screw. With strong bending of the cable has a break sneaking property, breaking and passing a part of the fiber module. More advanced cable design contain this bar, wearing a plastic shell: while it is more difficult to break and damage the cable when it is the turn will cause less. Bars and is the same as in the figure, and very thin. The tip of the bar - a great tool for fine abrasive work, for example, to clean relay contacts or a portion of the copper solder parts. If it burn for a couple of centimeters, you get a nice soft brush. smile.gif
2 - the optical fibers themselves (in the figure - in lacquer insulation). The very finest threads, fibers, for which all afoot. In this article we will speak only about the glass fibers, although somewhere in nature, there are plastic, but they are - great exotic, not cooked devices for welding optics (only mechanical connection) and are suitable only for very short distances and I personally did not face them . Optical fibers are single-mode and multimode, I have met with only single-mode, multimode since - outdated technology, it can only be used for short distances and singlemode perfectly replaced. The fiber consists of a glass "shell" made of glass with certain impurities (in chemistry and crystallography will not stop there, because they do not know the subject). Without varnish fiber has a thickness of 125 micrometers (slightly thicker hair), and in its center there is a core diameter of 10 microns high purity glass of different composition and slightly different from the cladding refractive index. It extends the core radiation (due to the effect of total reflection at the "core - shell"). Finally, on top of a 125-micrometer Cylinder "shell" covered by another shell - from a special varnish (clear or colored - for color-coded fibers), which is also a dual-layer EMNIP. It protects the fiber from moderate injuries (without varnish though fiber bends, but bad and easy to break, the fiber elementary crumble from a random position on his mobile phone; and the varnish can be safely wrapped around a pencil and pull strongly enough - it will stand). It happens that span cable slack on some fibers: broke (perezhglo, cut) all shell Kevlar burst central rod, and some 16 or 32 125 micron glass fiber can span weeks to keep the weight of the cable and wind loads! Nevertheless, even in the lacquer fibers can be easily damaged, so the fitter of the most important - the meticulousness and accuracy. One awkward movement can ruin the results of a day of work or, if not particularly lucky and there is no backup for a long time to drop the trunk link (if, digging in "combat" the main clutch, break the fiber DWDM-th under the spine at the outlet of the cable).
Fiber is a lot of varieties: ordinary (SMF or just SM), with dispersion shifted (DSF or just DS), a non-zero dispersion shifted (NZDSF, NZDS or NZ). Outwardly, they can not distinguish the difference - in the chemical / crystalline composition and, probably, in the geometry of the central core and the smoothness of the boundary between it and the shell (unfortunately, for themselves and do not clarify the matter before the end). Dispersion in optical fibers - a harsh and difficult to understand a thing, worthy of a separate article, so easy to explain - for dispersion shifted fiber can transmit a signal without distortion more than in the simple. In practice, the fitter know two types: simple and "with smeschёnkoy."The cable is often isolated the first module under the "smeschёnku" and the rest - a simple fiber. Docked "smeschёnku" and a simple fiber can be, but is not desirable, it is an interesting effect, which I will discuss in another part, about the measurement.
3 - plastic tube modules, which float in the hydrophobe fiber.
The cable to the split modules
Optical fibers,damagedas a result ofcarelesscutting a cable(waswronglyexposedblade lengthstripperto remove theinnersheath, causingeruptedmodulesand damageof the fibers)
In this picture-only apart of the "birth" and"species"opticalsockets
Wallcross-type16 portFC.By the way,cookedbadly:yellowshellP & G-Tailnotenter theCRSSand fiberscan break,and the fibersare laidin the cassettewith smallbending radii.
Workon the96cross-typeFCports
Oftenoptionandcheaper -whenthrownfrom thecrossall thatis possible,then it turns outsomething like this:
Reduced:93% of the [731to355]- Clickto viewfull image
undefined
Opencross8-porttypeSC / APC,1unit.WorsewhatP & Goptical-Tailare not protectedandtheycanbreakthose whowilldelve into thedrawer/front,dragging, say,a new cable.
All thesecrossesare mountedin a rack, but there areoptions forwall,and otherrare.
↧
↧
Neuwicklung Generator, 800 KVA, 5,2 KV, 750 rpm / min
↧
High Voltage Motor rewinding "ELIN" 6.2 KV 2 separate windings: 1.485 and 985 rpm / min, 900 per 245 KW
↧
Spraying metal powder. Edit Required Shaft dimension
↧
Rewinding a low voltage generator 225 KVA, 14 pol., 400 V
↧
↧
Sulfuric Acid Handling Equipment Instrumentation Materials of Construction Inspection Procedures
Sulfuric Acid
Handling EquipmentInstrumentation
Materials of Construction
Inspection Procedures
Q.
What kind of pump do you use to transfer acid from the tank to the process?
A.
A centrifugal, sealless magnetic-drive pump is the preferred pump for sulfuric acid transfer. The wetted parts should be 316 stainless steel, Alloy 20 or Teflon®-lined.
Q.
What kind of metering pump is used for small quantities if acid (<5 br="" gpm="">A.
Positive displacement pumps, with wetted parts of Alloy 20, 316 stainless steel or Teflon® are typically used for this application.
Q.
What do you recommend for piping?
A.
The materials of construction for piping are dependent on fluid flow velocities and quality concerns. In general, seamless carbon steel piping is used for flow velocities between 1-3 feet per second (fps). 316 SS is acceptable for flow velocities of 0-8 fps. Alloy 20 works for flow velocities of 0-20 fps, and Teflon®-lined pipe works for all ranges of fluid velocity. If iron contamination is a concern for the process, stay away from carbon steel.
These recommendations assume ambient temperatures. All metal piping should be welded per "ANSI B31.3 - Normal Service" specifications.
Screwed fittings are discouraged. PVC and CPVC piping is recommended for vent/vapor lines only. They are not recommended for liquid service.
Q.
What do you recommend for storage tanks?
A.
The most common material used for sulfuric acid (>70%) storage tanks is carbon steel. It is relatively inexpensive and offers good corrosion resistance. If iron contamination is a problem in your process, 304 or 316 stainless steel is acceptable. For more aggressive environments, Alloy 20
may be an economical choice. For small tanks (<4500 95="" acid="" be="" below="" br="" concentrations="" cross-linked="" gallons="" high-density="" may="" polyethylene="" suitable.="" sulfuric="" with="">Q.
Are vertical or horizontal tanks better?
A.
Both horizontal and vertical tanks can give good service as a sulfuric acid storage tank if properly designed and maintained.
Q.
Are PVC and/or CPVC acceptable for sulfuric acid?
A.
PVC and CPVC are acceptable only for vent line or overflow line piping.
PVC and CPVC chemically will withstand exposure to sulfuric acid. They are not recommended for liquid service, though, as the plastic pipe does not have adequate "mechanical strength" to hold the sulfuric acid (remember,
the acid weighs almost twice as much as water) and is subject to mechanical failure.
Q.
Is Teflon® OK for sulfuric acid?
A.
All grades of Teflon® are acceptable for all strengths of sulfuric acid up to 400° F.
Q.
What do you recommend for valves?
A.
Plug valves or full-port ball valves are generally recommended for sulfuric acid service. Valves should be constructed of cast Alloy 20 for acid strength above 70%.
Q.
What kind of hoses are OK for sulfuric acid?
A.
A Teflon® PTFE-lined hose is acceptable for 93-98% sulfuric acid service.
The hose should be designed with a 200-psi minimum working pressure and be full vacuum rated. The end fittings must be crimped or swaged - banding is not recommended. The hose manufacturer must list the hose as "satisfactory" for 93-98% sulfuric acid service. The hose end fittings should
be 316 stainless steel with flanges or quick-connect fittings. The gasket must be virgin Viton® B. The user should have a "hose management program" in place to ensure the integrity of the hose. The hose must be dedicated to sulfuric acid service.
Instrumentation
Q.
What level gauges work for acid storage tanks?
A.
Several different types of level gauges will give satisfactory service for sulfuric acid storage tank levels. These include differential pressure (d/P) cells, sonar probes, radar probes, capacitance probes and floats. The "wetted" parts should be 316 stainless steel, Alloy 20 or Teflon®-lined.
Q.
What kind if flow meters work?
A.
Several types of flow meters will work with sulfuric acid, including:
magnetic flow meters, coriolis (mass flow) meters (Micro Motion), armored rotameters and ultrasonic flow meters. All of these can give adequate service for sulfuric acid.
Q.
Are there any in-line acid strength meters that work?
A.
In-line acid strength analyzers can be designed for sulfuric acid service.
Ones that have had success include sonic velocity analyzers, conductivity analyzers, refractive index analyzers and density meters. All of these analyzers can "flip-flop" at some acid strengths and give erroneous readings (conductivity at ~100%, sonic velocity at ~100%, refractive index at ~100%
and density at ~97%).
Q.
Are sight glasses in the piping acceptable?
A.
Sight glasses can be successfully used in sulfuric acid piping systems. Care must be taken to ensure they are protected from mechanical damage and are constructed of suitable materials.
Q.
Do you need dry air or nitrogen for bubbler level gauges?
A.
Dry instrument air (dew point <-40 acid="" added="" are="" br="" bubblers.="" corrosivity="" f="" for="" increases="" its="" metals.="" moisture="" most="" nitrogen="" only="" or="" preferred="" sulfuric="" to="">Materials of Construction
Q.
What are the limits of carbon steel in acid service?
A.
In general, carbon steel is the most commonly used material of construction for storage tanks and piping with sulfuric acid above 77%. In piping care must be taken to design the piping system to minimize turbulence in the liquid flow. The piping should be sized to maintain fluid velocity between 1-
3 feet per second (fps). Schedule 80 (minimum) welded piping is recommended. The temperature should be kept below 100° F wherever possible. For tanks, the design corrosion allowance should be 1/8".
Q.
When should I use stainless steel vs. carbon steel?
A.
Stainless steel should be used in place of carbon steel if iron contamination is a problem in your process. Also, stainless steel is acceptable for 100 sulfuric acid - carbon steel is not. Stainless steel is also preferred at low (<20 a="" acid="" br="" concentrations.="" greater="" grooving="" has="" hydrogen="" resistance="" stainless="" steel="" to="">Q.
Is copper/brass/bronze OK with acid?
A.
Copper/brass/bronze is not acceptable for sulfuric acid service, at any strength.
Q.
Is glass OK?
A.
Glass has excellent corrosion resistance with sulfuric acid, at all concentrations.
Q.
What is the corrosion mechanism with acid and steel?
A.
When sulfuric acid first contacts carbon steel, iron sulfate (FeSO4) is produced. The iron sulfate coats the steel and forms a "passivation" film which then protects the carbon steel from further corrosion. Flammable hydrogen gas (H2) is also produced by the corrosion reaction:
Fe(S) + H2SO4(l) --> FeSO4(s) + H2(g)
Q.
What are the temperature limits of steel, stainless steel and Alloy 20 in acid service?
A.
For steel the temperature should be maintained below 100° F, for stainless steel below 120°F , and for Alloy 20 below 140° F.
Q.
Is Hastelloy® OK?
A.
Hastelloy® B and C are generally acceptable for most strengths of sulfuric acid. They are usually only used for specialty applications, as it is ~6X the cost of carbon steel.
Q.
Is PE and/or PP OK? At what temperature and %?
A.
Polyethylene (PE) and polypropylene (PP) have limited applications in sulfuric acid service. PE can be used for small (<5000 95="" acid="" ambient="" and="" at="" below="" br="" cross-linked="" density="" for="" gallon="" high="" is="" pe="" preferred="" resin="" storage="" sulfuric="" tanks.="" tanks="" temperatures="" the="">Polyethylene can be used for sample bottles, drums and tote tanks at the same conditions. PP is slightly more resistant to sulfuric acid than PE in the 95-98% range, at ambient temperatures. Both plastics may be subject to stress cracking - the potential increases with temperature, storage time and strength.
Q.
What is “hydrogen grooving”?
A.
When sulfuric acid first contacts carbon steel, a passivation coating of iron sulfate is formed, along with hydrogen gas. The iron sulfate coating protects the steel from further corrosion. The hydrogen gas bubbles will float up in the liquid sulfuric acid. If, as the H2 bubbles float up, they contact the metal, the bubbles will scrape off the iron sulfate coating, exposing bare metal.
This will form more iron sulfate and more H2 bubbles. The bubbles tend to follow the same track, exposing more bare metal. Eventually the metal will have grooves corroded/eroded into the surface from the "never-ending" cycle of iron sulfate formation/H2 "scrubbing bubbles"/bare metal/iron sulfate formation. The striation in the metal is called "hydrogen grooving".
Q.
Why does piping develop leaks at elbows and/or welds?
A.
For carbon steel piping, the recommended fluid velocity is 1-3 feet per second (fps). Below 1 fps the corrosion phenomena called "hydrogen grooving" takes place. Above 3 fps, generalized corrosion will occur. In sulfuric acid service, the carbon steel is protected from corrosion by a passivation coating of iron sulfate. If the fluid velocity exceeds 3 fps, the iron sulfate passivation coating does not form. In piping transition pieces (elbow, tees, valves, expansion, contraction, etc.) the fluid velocity tends to be greater (because of turbulence) than in the straight pieces of pipe, so the passivation coating does not form as well. Also, downstream of welds, if there is any slag left inside the pipe, turbulence tends to occur, and the iron sulfate coating doesn't form well. With less passivation coating, generalized corrosion is accelerated in those spot.
Q.
What are the flow limitations for acid piping?
A.
The "Rules of Thumb" for flow limitation when designing piping system at ambient temperatures are:
• Carbon Steel: 1-3 feet per second (fps)
• 304 and 304L stainless steel: 0-6 fps
• 316 and 316L stainless steel: 0-8 fps
• Alloy 20: 0-20 fps
• Teflon® and Kynar® lined: 0-50 fps
Inspection Procedures
Q.
How do you inspect an acid storage tank?
A.
There are three types of inspections normally done on a sulfuric acid tank.
The first is an external "walk-around" inspection.
• Every year someone should "walk-around" the tank, looking for signs of sulfate leakage or other metal deterioration, making sure the insulation (if so equipped) is weather-tight, observing the overflow/vent line to make sure it is not plugged, looking at the tank foundation/supports.
• A more thorough external tank inspection would include an ultrasonic thickness test. Areas around welds and nozzles should be carefully reviewed
• An internal tank inspection is the most thorough. It involves emptying and cleaning the tank. Someone (preferably an API-certified inspector) then enters the tank and visually inspect the internal welds and tank surfaces. Ultrasonic thickness testing should be done on the floor and any other questionable areas at this time. Be sure to follow all OSHA guidelines when entering the tank.
Q. How often do you inspect an acid storage tank?
A. General guidance for tank inspections is as follows:
• An annual external "walk-around" inspection.
• A biennial ultrasonic thickness test.
• Every 5-6 years empty and clean the tank, and internally inspect the tank. These inspection frequencies can be increased or decreased, based on actual findings when the tanks are inspected. Be sure to document all inspections and keep copies in the tank files. Use API 653 for
guidance on vertical tank inspections.
Q. 5000>20>-40>4500>5>
How do you inspect piping? How often?
A.
In general, piping is formally externally inspected visually every five years, and ultrasonic thickness tested biennially. Again, actual plant experience may dictate an increase or decrease in this schedule. Extra attention should be paid to elbows, tees, valves and any other places in the piping where flow disturbances (and erosion/corrosion) could occur. Use API 570, Class II piping standards for guidance.
Q.
How do you clean an acid tank?
A.
Sulfuric acid tanks are usually only cleaned when the tanks are due for the internal inspection (every 5-6 years) or when the iron sulfate builds-up in the tank enough to cause quality problems with the product.
Sulfuric Acid Process
Q. How do you make sulfuric acid?
A. The primary process used to make sulfuric acid is called the "Contact Process". Molten sulfur is sprayed through an atomizer nozzle into the sulfur burner and combusted with dry air to make sulfur dioxide (SO2). The air is dried by running it countercurrent through a spray column filled with sulfuric acid. The acid absorbs all moisture in the air. The SO2 gas is passed through a multi-layer catalytic converter with more air to make sulfur trioxide (SO3). The catalyst used is vanadium pentoxide. The SO3 gas is absorbed in sulfuric acid to make a higher strength (tower) sulfuric acid. The tower acid is then blended with water to get the desired sales strength.
Q. What do use for materials of construction in your plant?
A. Carbon steel is the most commonly used material in a sulfuric acid plant.
Q. What are the raw materials for sulfuric acid?
A. The basic raw materials for sulfuric acid are sulfur, air and water. The sulfur can be from elemental sulfur, from H2S, or roasted from metal sulfides.
↧
Sulphric Acid - Manufacturing process
Manufacturing process -1
Image may be NSFW.
Clik here to view.
In front of SRG burner & WHB, Baoshan Steel Mill, Shanhai, China
Overview : Classify general sulfuric acid manufacturing process and it will be the following.
1. Classification by raw material 1) sulfur combustion type ... oil recovery sulfur and sulfur raw material 2 of high purity (99.9% or more)) or gold type ... copper, zinc, 3 for the refining gas and sulfide iron ore, such as nickel as a raw material ) Other raw materials ... coke oven gas desulfurization sulfur, the sour gas, flue gas desulfurization recovery SO2, 2, such as waste sulfuric acid decomposition gas. Classification by conversion (simple contact and double-contact) 3. Or energy recovery-oriented or construction costs emphasis
In addition, as a special process
1) wet method 2) non-stationary converter 2) WSA method 3) SULFOX method
I have.
General process: A) raw materials
Sulfur combustion: Modern sulfuric acid manufacturing process, are all "contact". Production method of this is, go through basically the "burning", "conversion" three-step reaction of "absorption".
1) If sulfur to generate the combustion = SO2 (sulfur oil recovery) is the raw material: S + O2 → SO2
2) oxidizing the conversion = SO2 to SO3 and
SO2 + 1 / 2O2 → SO3 (at converter)
3) The absorption = SO3 is reacted with water to produce sulfuric acid H2SO4
SO3 + H2O → H2SO4
Metallurgy formula: → "Introduction", "raw material"reference material is chalcopyrite, in the case of" metallurgy expressions "such as iron sulfide, because it contains a large amount of metal oxide dust during the roasting gas,
1) If the combustion chalcopyrite is of raw materials: 4CuFeS2 + 9O2 → 2Cu2S + 2Fe2O3 + 6SO2 (in smelting furnace) Cu2S + O2 → 2Cu + SO2 (at BOF)
2) removing the metal oxide by a gas purification dry, wet dust collector, to obtain a clean gas.
3) The same 4 and conversion ... sulfur combustion type) the same as the absorption ... sulfur combustion
Other Ingredients: It has clean ones and dirty ones by the raw materials.
Clean SO2 gas (recovery from wells Man load method flue gas desulfurization SO2) → gas drying, conversion, only the absorption of equipment dirty gas -1 (coke oven gas recovery sulfur, the sour gas, such as waste sulfuric acid) → about the same device used dirty gas and metallurgy type-2 (activated coke method desulfurization recovery SO2) → The "dirty gas -1" of the combustion device is not, "gas purification" and later, almost the same as the metallurgy formula
Other Although it is currently unclear whether also are driving, the process of obtaining the SO2 gypsum by thermal decomposition had been adopted in the former communist bloc. Today, we have seen plaster and clay, the process of manufacturing the SO2 and cement clinker from silica sand in the literature overseas.
"Whether used as a raw material?", You can consequence to all "whether profitable". Currently a good recovery sulfur purity can get at low cost, iron sulfide is not used. However, down the purity of the copper and nickel ore, and now that hydrometallurgy have been widely used, refining = increase of sulfuric acid usage (the selfish, refining = was a byproduct of sulfuric acid) it becomes. Of sulfide iron ore, there may be a re-turn.
B) conversion
When you want to increase the conversion rate, method called double-contact (double contact) is best. This course of 2) above, the partially converted gases in the converter to reduce the SO3 By intermediate absorption is intended to increase the overall conversion by conversion and absorption is fed back to converter. In other words, as compared to a normal (single-contact) system, an intermediate absorber tower and the pump tank for the circulating pump, a cooler, and becomes like the need gas heat exchanger for re-heating. The final conversion rate, it depends on the conditions, but is that of a possible 99.9%.
However, in this method, part of the gas sensible heat exiting the converter is absorbed by the acid intermediate absorber tower, since it is released into the cooling water, the recovery amount of energy will be the decrease in comparison with the single-contact .
It does not lead to so much of the conversion, as a way to increase in the same manner as the conversion rate, option is to use a cesium strengthening catalyst, but the placement of the equipment because this case is a single contact is immutable.
C) energy recovery or construction costs?
Burning sulfuric equipment, conversion, all of the processes of absorption since exothermic reaction, is possible to recover the heat in the form of such steam and electricity. This is how to recover to the fullest, or recovery is also the choice of either reduce the construction costs by suppressing.
S (c) + O2 (g) → SO2 (g) + 301.89kJ / mol (combustion) SO2 (g) + 1 / 2O2 (g) → SO3 (g) + 98.87kJ / mol (conversion) SO3 (g) + H2O (l) → H2SO4 (l) + 132.46kJ / mol (absorption)
If you want to focus on energy recovery:
Recovery conversion heat in waste heat boiler of the combustion heat → combustion furnace exit → converter around the waste heat boiler, economizer, super heater, use the boiler feed water to cool the heat of absorption → circulation acid in the air preheater, or We installed a heat recovery system, such as HRS and HEROS. * 1
* 1: HRS US MECS , Inc., HEROS Germany Outotec in the system recommended by the company, to recover the heat of absorption of both SO3 as low-pressure steam.
Moreover, by increasing as much as possible the concentration of the sulfur combustion furnace exit gas, there is also effective to raise the gas temperature. By placing the air blower in the back of the drying tower, it is also possible to recover the heat of compression as an increase of the combustion gas temperature.
If you want to reduce the construction costs:
Cheap Toka there is no consumption destination be recovered vapor or power, or in large-scale plants such as when the device itself is large and expensive, you should reduce the construction costs. The adjustment of the inlet temperature of the converter layers, dry air of the drying tower exit (in the case of refining gas, dry gas SO2) by bubbling, omit the heat exchanger. Furthermore, cooling the gas surrounding the converter by air-cooled heat exchanger, the heated air is released into the atmosphere without heat recovery.
Combustion furnace exit gas it is thought that there is no choice but to cooling in the waste heat boiler, which also reduces the boiler by raising the boiler outlet temperature, it can also be followed by air cool. The pyrite raw material plant in Africa certain country for the roasting furnace exit gas is quenched with water, it was manner which is not at all heat recovery.
Course construction costs if small whole plant equipment will drop. In this case raise the ventilation resistance, so you will need a great deal of power in the blower, to drive the blower in a steam turbine that uses the recovery steam. Ventilation resistance of the entire plant, but was about conventional 35KPa, of recently, it is an example also become 45KPa ~ 70KPa especially in large plants.
Drying tower and the absorption tower but should differ from the original circulation acid concentration, it has also been put to practical use to circulate the same 98% of the sulfuric acid in the pump tank in common. In this case, we need a single concentration controllers and liquid level controllers also not only the pump tank is reduced. I do not have experience.
Manufacturing process -2
Sulfur combustion:
Sulfur combustion -1 :
The accompanying drawings "PFD-1 Please refer to the ". Is this,
• The molten sulfur raw materials and a single contact as much as possible to minimize the cost (energy recovery is not much need)
This is an example of the case.
Molten sulfur is supplied to the sulfur combustion furnace at the pump. Combustion air, after removing the H2O in the gas by contacting the drying tower in 93 ~ 95% H2SO4, will be sent to the sulfur burner. In this flow blower it has been installed in front of the drying tower. Because this person is you can use the carbon steel as the material of the blower, the equipment cost will decrease. Sulfur is burned in the combustion furnace, SO2 - it becomes (10.5 12%). At this time, the gas temperature in the combustion heat will be 1,050 ℃ ~ 1,200 ℃.
S (c) + O2 (g) → SO2 (g) + 301.89kJ / mol
At the same time, it is a small amount in the furnace, but is said to occur also byproduct of SO3 and NO / NO2.
The hot gas is cooled in the waste heat boiler is recovered heat is simultaneously in the form of steam.
The converter inlet temperature, because the action of the catalyst to optimize the 430 ℃ before and after said (if normal vanadium catalyst) to control by adjusting the bypass valve opening degree of the waste heat boiler.
Converter has a catalyst layer of 3-5 stages, usually four stages. Here, the SO2 is oxidized to SO3, because each layer outlet temperature by oxidation heat rises, it does not go not to cool down before it enters the next layer to 430 ℃ or less.
SO2 (g) + 1 / 2O2 (g) → SO3 (g) + 98.87kJ / mol
To reduce the cost of equipment, it is blown to the catalyst layer a low dry air temperature in the conversion, to lower the inlet temperature. It (the case of four-layer) is often placed in a single layer outlet and the three-layer outlet. The inclusive air blowing, such as gas heat exchange and boiler of this part I will be measured reduction of construction cost is unnecessary. Furthermore surplus of heat, indirect cooling, and removed in the air by the gas cooler.
This process is a single contact late final conversion rate is 96-97 percent, by using, for example, cesium strengthening catalyst, depending on the conditions, it is also possible to 99%.
Gas from the converter absorbs the SO3 in the gas in the absorption tower at 98 ~ 98.5% H2SO4, get the product concentrated sulfuric acid by the circulation acid rose concentration is diluted with water.
SO3 + nH2SO4 · H2O → (n + 1) H2SO4
Summary
SO3 (g) + H2O (l) → H2SO4 (l) + 132.46kJ / mol
Part of the absorption tower circulating sulfuric acid, will be taken out as a product to the outside of the system. Although not shown in this flow, winter dilution equipment for diluting the product sulfuric acid concentration to 95%, and product cooler comes after this.
Exhaust gas from the absorption tower, SOx in the gas are absorbed and removed by an exhaust scrubber. There are different types of scrubber, but alkali absorption is common. It is not shown in the flow, but you might want to set up a mist Cottrell (wet electrostatic precipitator)) as white smoke measures of exhaust.
In addition, we have omitted to flow, the converter is the one often preheating furnace for the start TokiNoboru temperature is included.
By the way, the preheating of sulfur combustion furnace, heavy oil for preheating the oven (or, LPG) is done by direct heating and comes with a burner.
Sulfur combustion -2 :
PFD-2 please see. Is this
I for the purpose of a-molten sulfur feedstock · DC / DA (double contact double absorption method) and energy recovery increased
It is the case. Of the above-mentioned PFD-1 please compared to.
Air blower is installed after the drying tower, heat of compression of the air is supplied to the combustion gas, it has to be able to recovery. SO2 oxidation heat of the converter, in part, but has been used to raise the temperature of the return SO2 gas from the intermediate absorption tower, it is used to preheat the feed water to the boiler. In addition, to make the superheated steam, This will not drive the air blower.
The recovery of SO3 absorption heat of the intermediate absorption tower, we have established a HRS tower to cool the circulating acid, with the aim of recovery of medium- and low-pressure steam.
Manufacturing process -3
Examples:
Metallurgy type process:
The accompanying PFD-3 Please see. It has drawn sulfide iron ore, copper, zinc, nickel concentrate (both sulfide) as a raw material of the process of "metallurgy expressions". Even if you want to desulfurization recovered sulfur, such as desulfurization recovery H2S gas as a raw material, it is the same basically. Similar to the aforementioned process-2, Targeting · DC / DA Law and energy recovery increase
Thing.
Although not described in detail here, in "dry gas purification", the cyclone and dry electrostatic precipitator (hot Cottrell), but the part of the "wet gas purification" various scrubber and wet electrostatic precipitator (mist Cottrell) It is included. In this part, to remove the dust in the gas from the roasting furnace, purpose is to obtain a clean SO2 gas. When arsenic and mercury in the raw material, is halogen and said substance is included, we can set up a dedicated removal equipment of each. Examples of the wet scrubber There are many things but, MECS, Inc. has focused on DynaWave.
Gas became clean enters the drying tower, it will remove absorb the H2O in the gas. From drying tower entrance is allowed to suck the air, and then the converter entrance of the O2 / SO2 ratio = ~ 1.2.
After this is basically does not change with the aforementioned sulfur combustion type, for gas passes through the purification system and the drying tower, the temperature has dropped to about 40 ℃, the catalytic reaction in the converter this optimal ~ 430 ℃ to cause the order to (usually the case of the catalyst) heated up, you can use the SO2 oxidation heat in the converter. Specifically, it is heated by causing the outlet gas and the heat exchange from the respective layers.
Absorption tower and Jogai-to after this is the same as the sulfur combustion.
For the conventional method, it is often becomes low SO2 concentrations in the converter inlet as compared to the sulfur combustion. Hence, the furnace recent metallurgical expression by suppressing the increase of the unreacted N2 components by using oxygenation air mixing oxygen into the combustion air, to lower the SO2 concentration, and those that do not increase the amount of gas It seems there are many. Such as in the case of sour gas from a conventional method and COG, it will not be able to raise the temperature of the gas entering the oxidation heat in too low, the converter. In this case, you need to'll supplemented with heat from outside continuously.
This, whether or not heat balance can take, you can be judged by the following formula.
Blower outlet (the first heat exchanger shell side inlet) gas sensible heat = Q1 Absorption tower entrance (the first heat exchanger tube side exit) gas heat = Q2 The SO2 → SO3 oxidation heat = Q3 in the converter
In
Q1 + Q3> Q2
Heat balance will take so long. However, because there is heat loss from the device surface of the converter system, in fact
(Q1 + Q3) * 0.9> Q2
It is safe if as a.
Other raw materials:
Clean flue gas desulfurization gas
PFD-4 please see. This is recovered from flue gas desulfurization equipment, such as Wellman Road Law, is the SO2 gas of high concentration in high purity (However, water vapor saturation). Since there is no need of gas purification, gas after removal of the H2O in the direct drying tower, will be sent to the converter. Because usually high SO2 concentration, you need to or use high-density catalyst or diluted with air. Exhaust of the absorption tower, so returned to the flue gas desulfurization gas, not necessarily the high conversion is required.
Dirty gas -1 (desulfurization sulfur waste liquid, waste sulfuric acid, containing H2S gas, etc.)
PFD-5 Please refer to. These raw materials, it is necessary to generate SO2 by first combustion. Because of course it combustion heat is generated, and the waste heat boiler is provided by a heat recovery in the form of steam. After that, it will remove the dust of gas was cooled and the gas at the gas purification equipment. After drying tower is the same as PFD-4, but the exhaust is released into the atmosphere after it was treated with a scrubber. Usually, because SO2 concentration is low, measures must be taken to reduce the H2O in the process gas.
Dirty Gas 2 (flue gas desulfurization gas containing dust)
PFD-6 Please refer to. This is because, as of activated coke law, those containing dust in the recovery SO2 gas, combustion furnace is not required gas purification equipment is necessary. Except there is no combustion furnace is the same apparatus sequence as a "dirty gas -1". However, because SO2 concentration is higher in the case of this gas, it will be rather necessary dilution with air.
Manufacturing process -4
Special process:
Wet method:
Whether the other raw materials any sulfur combustion, the catalytic reaction gas in the generic process is supplied to the converter does not contain H2O. This is to avoid the risk of equipment corrosion and stop time of the catalyst damage. The drying tower is used for the purpose, it has been absorbed and removed the H2O contained by washing the sulfur combustion air and process gas after the gas purification unit in the 93 ~ 95% H2SO4. However, there is also a process of contacting reaction while containing H2O in the gas. This is usually the gas in the beautiful but is also small equipment SO2 concentration is thin production volume, and the product will be only adopted in special conditions that may be a dilute sulfuric acid. Requires no drying tower as equipment, after the converter, the condenser and the cost of equipment and the electrical dust collector is only in place of the absorption tower is you can be kept low. However, because of that can not be concentrated sulfuric acid is that the application of the product is naturally limited, example that has now been adopted it seems that little.
WSA method:
A type of the above-mentioned wet method, but without causing total amount of condensed H2O in the gas, a method of obtaining a high concentration of sulfuric acid by partial condensation, Harudatopuso Inc. (Denmark) was developed in the mid 1980s. Gas containing H2O is oxidized SO2 is directly at the converter, the generated SO3 is a gaseous H2SO4 reacts with H2O. This H2SO4 vapor by partial condensation in a glass condenser to get the concentrated sulfuric acid. Oxidation heat generated by the converter will be recovered by the molten salt boiler. Concentrated sulfuric acid concentration of purification is determined by the H2O content in the gas. If 10% or less, Toka it possible to obtain 98% H2SO4. Moreover, by changing the SO3 Gasugu H2SO4 generated by converter, so remains SO3 concentration in the gas is always low, it means that same equilibrium with DC / DA method is shifted to the side to promote the oxidation of SO3, the final conversion Toka equal to or greater than 99%. Originally, the simple contact-type exhaust sulfuric equipment, such as boiler combustion gases, it was a process for producing sulfuric acid from a very thin SO2 concentration of the gas, at present, it and the high density SO2 from metallurgical type roasting furnace gas, H2S from oil refining, coke oven gas purification H2S, sulfur sludge, such as waste sulfuric acid and sulfuric acid drainage from the petrochemical, can accommodate a wide variety of raw materials, there is a construction track record 100 groups close to the world. In Japan, there was a facility from the petrochemical waste sulfuric acid, it is not currently for the generation process of the waste acid was discontinued. Globally, we have argued that already have a track record of more than 130 groups. (November 2014 currently) As compared with the general process, also in the plant cost, advantageous and manufacturers in the utility surface (Topuso Inc.) has claimed. However, in the molten sulfur raw materials, the original wet method because moisture is less in the air benefits I will think less. Also in the non-ferrous metal smelting, because the cost of the furnace and the gas purification part is greater than the sulfuric acid production facility, it will presumably cost benefit is small compared to other sulfur source. → WSA schematic flow→ experience in smelting gas Direction you are interested contact us please. Topuso's Japanese distributor, we will introduce the OTC.
SULFOX method:
those MECS, Inc. has developed, like the WSA method, it is wet sulfuric acid production process. It unique in this process, not only a thin SO2, is that it is a can produce sulfuric acid by oxidation in the converter within the catalyst also the H2S gas. Again by adjusting the condensing temperature? It obtained a high concentration of sulfuric acid, and then you have.
Non-stationary converter:
The catalyst of the converter is not divided into multiple stages, in a manner that switching between the entrance and exit of SO2 gas at regular time intervals, it is that you omit the converter around the gas heat exchanger. After preheating the catalyst, when you through the cold SO2 gas from the catalyst top, because among the first is the catalyst temperature oxidation start temperature or higher SO2 + 1 / 2O2 → SO3 Reaction of go, but you have cold gradually gas inlet side. If the gas inlet is now switch to from the catalyst bottom, the oxidation by touching the high temperature of the catalyst is continued, catalyst upper part which has been cold will be heated by the heat of reaction. If you have cold the bottom, now also conducts SO2 gas from the top ... If you continue this reaction sufficient conversion rate is obtained, thing.
It is a technology that has been developed in the former Soviet Union, there was operational cases until recent years in China. But the will not big final conversion rate is obtained, it is questionable whether really stable conversion rate can be maintained. In Japan there was a engineering company that sells this technology, but it does not have heard the story that was sold.
Image may be NSFW.
Clik here to view.

Overview : Classify general sulfuric acid manufacturing process and it will be the following.
1. Classification by raw material 1) sulfur combustion type ... oil recovery sulfur and sulfur raw material 2 of high purity (99.9% or more)) or gold type ... copper, zinc, 3 for the refining gas and sulfide iron ore, such as nickel as a raw material ) Other raw materials ... coke oven gas desulfurization sulfur, the sour gas, flue gas desulfurization recovery SO2, 2, such as waste sulfuric acid decomposition gas. Classification by conversion (simple contact and double-contact) 3. Or energy recovery-oriented or construction costs emphasis
In addition, as a special process
1) wet method 2) non-stationary converter 2) WSA method 3) SULFOX method
I have.
General process: A) raw materials
Sulfur combustion: Modern sulfuric acid manufacturing process, are all "contact". Production method of this is, go through basically the "burning", "conversion" three-step reaction of "absorption".
1) If sulfur to generate the combustion = SO2 (sulfur oil recovery) is the raw material: S + O2 → SO2
2) oxidizing the conversion = SO2 to SO3 and
SO2 + 1 / 2O2 → SO3 (at converter)
3) The absorption = SO3 is reacted with water to produce sulfuric acid H2SO4
SO3 + H2O → H2SO4
Metallurgy formula: → "Introduction", "raw material"reference material is chalcopyrite, in the case of" metallurgy expressions "such as iron sulfide, because it contains a large amount of metal oxide dust during the roasting gas,
1) If the combustion chalcopyrite is of raw materials: 4CuFeS2 + 9O2 → 2Cu2S + 2Fe2O3 + 6SO2 (in smelting furnace) Cu2S + O2 → 2Cu + SO2 (at BOF)
2) removing the metal oxide by a gas purification dry, wet dust collector, to obtain a clean gas.
3) The same 4 and conversion ... sulfur combustion type) the same as the absorption ... sulfur combustion
Other Ingredients: It has clean ones and dirty ones by the raw materials.
Clean SO2 gas (recovery from wells Man load method flue gas desulfurization SO2) → gas drying, conversion, only the absorption of equipment dirty gas -1 (coke oven gas recovery sulfur, the sour gas, such as waste sulfuric acid) → about the same device used dirty gas and metallurgy type-2 (activated coke method desulfurization recovery SO2) → The "dirty gas -1" of the combustion device is not, "gas purification" and later, almost the same as the metallurgy formula
Other Although it is currently unclear whether also are driving, the process of obtaining the SO2 gypsum by thermal decomposition had been adopted in the former communist bloc. Today, we have seen plaster and clay, the process of manufacturing the SO2 and cement clinker from silica sand in the literature overseas.
"Whether used as a raw material?", You can consequence to all "whether profitable". Currently a good recovery sulfur purity can get at low cost, iron sulfide is not used. However, down the purity of the copper and nickel ore, and now that hydrometallurgy have been widely used, refining = increase of sulfuric acid usage (the selfish, refining = was a byproduct of sulfuric acid) it becomes. Of sulfide iron ore, there may be a re-turn.
B) conversion
When you want to increase the conversion rate, method called double-contact (double contact) is best. This course of 2) above, the partially converted gases in the converter to reduce the SO3 By intermediate absorption is intended to increase the overall conversion by conversion and absorption is fed back to converter. In other words, as compared to a normal (single-contact) system, an intermediate absorber tower and the pump tank for the circulating pump, a cooler, and becomes like the need gas heat exchanger for re-heating. The final conversion rate, it depends on the conditions, but is that of a possible 99.9%.
However, in this method, part of the gas sensible heat exiting the converter is absorbed by the acid intermediate absorber tower, since it is released into the cooling water, the recovery amount of energy will be the decrease in comparison with the single-contact .
It does not lead to so much of the conversion, as a way to increase in the same manner as the conversion rate, option is to use a cesium strengthening catalyst, but the placement of the equipment because this case is a single contact is immutable.
C) energy recovery or construction costs?
Burning sulfuric equipment, conversion, all of the processes of absorption since exothermic reaction, is possible to recover the heat in the form of such steam and electricity. This is how to recover to the fullest, or recovery is also the choice of either reduce the construction costs by suppressing.
S (c) + O2 (g) → SO2 (g) + 301.89kJ / mol (combustion) SO2 (g) + 1 / 2O2 (g) → SO3 (g) + 98.87kJ / mol (conversion) SO3 (g) + H2O (l) → H2SO4 (l) + 132.46kJ / mol (absorption)
If you want to focus on energy recovery:
Recovery conversion heat in waste heat boiler of the combustion heat → combustion furnace exit → converter around the waste heat boiler, economizer, super heater, use the boiler feed water to cool the heat of absorption → circulation acid in the air preheater, or We installed a heat recovery system, such as HRS and HEROS. * 1
* 1: HRS US MECS , Inc., HEROS Germany Outotec in the system recommended by the company, to recover the heat of absorption of both SO3 as low-pressure steam.
Moreover, by increasing as much as possible the concentration of the sulfur combustion furnace exit gas, there is also effective to raise the gas temperature. By placing the air blower in the back of the drying tower, it is also possible to recover the heat of compression as an increase of the combustion gas temperature.
If you want to reduce the construction costs:
Cheap Toka there is no consumption destination be recovered vapor or power, or in large-scale plants such as when the device itself is large and expensive, you should reduce the construction costs. The adjustment of the inlet temperature of the converter layers, dry air of the drying tower exit (in the case of refining gas, dry gas SO2) by bubbling, omit the heat exchanger. Furthermore, cooling the gas surrounding the converter by air-cooled heat exchanger, the heated air is released into the atmosphere without heat recovery.
Combustion furnace exit gas it is thought that there is no choice but to cooling in the waste heat boiler, which also reduces the boiler by raising the boiler outlet temperature, it can also be followed by air cool. The pyrite raw material plant in Africa certain country for the roasting furnace exit gas is quenched with water, it was manner which is not at all heat recovery.
Course construction costs if small whole plant equipment will drop. In this case raise the ventilation resistance, so you will need a great deal of power in the blower, to drive the blower in a steam turbine that uses the recovery steam. Ventilation resistance of the entire plant, but was about conventional 35KPa, of recently, it is an example also become 45KPa ~ 70KPa especially in large plants.
Drying tower and the absorption tower but should differ from the original circulation acid concentration, it has also been put to practical use to circulate the same 98% of the sulfuric acid in the pump tank in common. In this case, we need a single concentration controllers and liquid level controllers also not only the pump tank is reduced. I do not have experience.
Manufacturing process -2
Sulfur combustion:
Sulfur combustion -1 :
The accompanying drawings "PFD-1 Please refer to the ". Is this,
• The molten sulfur raw materials and a single contact as much as possible to minimize the cost (energy recovery is not much need)
This is an example of the case.
Molten sulfur is supplied to the sulfur combustion furnace at the pump. Combustion air, after removing the H2O in the gas by contacting the drying tower in 93 ~ 95% H2SO4, will be sent to the sulfur burner. In this flow blower it has been installed in front of the drying tower. Because this person is you can use the carbon steel as the material of the blower, the equipment cost will decrease. Sulfur is burned in the combustion furnace, SO2 - it becomes (10.5 12%). At this time, the gas temperature in the combustion heat will be 1,050 ℃ ~ 1,200 ℃.
S (c) + O2 (g) → SO2 (g) + 301.89kJ / mol
At the same time, it is a small amount in the furnace, but is said to occur also byproduct of SO3 and NO / NO2.
The hot gas is cooled in the waste heat boiler is recovered heat is simultaneously in the form of steam.
The converter inlet temperature, because the action of the catalyst to optimize the 430 ℃ before and after said (if normal vanadium catalyst) to control by adjusting the bypass valve opening degree of the waste heat boiler.
Converter has a catalyst layer of 3-5 stages, usually four stages. Here, the SO2 is oxidized to SO3, because each layer outlet temperature by oxidation heat rises, it does not go not to cool down before it enters the next layer to 430 ℃ or less.
SO2 (g) + 1 / 2O2 (g) → SO3 (g) + 98.87kJ / mol
To reduce the cost of equipment, it is blown to the catalyst layer a low dry air temperature in the conversion, to lower the inlet temperature. It (the case of four-layer) is often placed in a single layer outlet and the three-layer outlet. The inclusive air blowing, such as gas heat exchange and boiler of this part I will be measured reduction of construction cost is unnecessary. Furthermore surplus of heat, indirect cooling, and removed in the air by the gas cooler.
This process is a single contact late final conversion rate is 96-97 percent, by using, for example, cesium strengthening catalyst, depending on the conditions, it is also possible to 99%.
Gas from the converter absorbs the SO3 in the gas in the absorption tower at 98 ~ 98.5% H2SO4, get the product concentrated sulfuric acid by the circulation acid rose concentration is diluted with water.
SO3 + nH2SO4 · H2O → (n + 1) H2SO4
Summary
SO3 (g) + H2O (l) → H2SO4 (l) + 132.46kJ / mol
Part of the absorption tower circulating sulfuric acid, will be taken out as a product to the outside of the system. Although not shown in this flow, winter dilution equipment for diluting the product sulfuric acid concentration to 95%, and product cooler comes after this.
Exhaust gas from the absorption tower, SOx in the gas are absorbed and removed by an exhaust scrubber. There are different types of scrubber, but alkali absorption is common. It is not shown in the flow, but you might want to set up a mist Cottrell (wet electrostatic precipitator)) as white smoke measures of exhaust.
In addition, we have omitted to flow, the converter is the one often preheating furnace for the start TokiNoboru temperature is included.
By the way, the preheating of sulfur combustion furnace, heavy oil for preheating the oven (or, LPG) is done by direct heating and comes with a burner.
Sulfur combustion -2 :
PFD-2 please see. Is this
I for the purpose of a-molten sulfur feedstock · DC / DA (double contact double absorption method) and energy recovery increased
It is the case. Of the above-mentioned PFD-1 please compared to.
Air blower is installed after the drying tower, heat of compression of the air is supplied to the combustion gas, it has to be able to recovery. SO2 oxidation heat of the converter, in part, but has been used to raise the temperature of the return SO2 gas from the intermediate absorption tower, it is used to preheat the feed water to the boiler. In addition, to make the superheated steam, This will not drive the air blower.
The recovery of SO3 absorption heat of the intermediate absorption tower, we have established a HRS tower to cool the circulating acid, with the aim of recovery of medium- and low-pressure steam.
Manufacturing process -3
Examples:
Metallurgy type process:
The accompanying PFD-3 Please see. It has drawn sulfide iron ore, copper, zinc, nickel concentrate (both sulfide) as a raw material of the process of "metallurgy expressions". Even if you want to desulfurization recovered sulfur, such as desulfurization recovery H2S gas as a raw material, it is the same basically. Similar to the aforementioned process-2, Targeting · DC / DA Law and energy recovery increase
Thing.
Although not described in detail here, in "dry gas purification", the cyclone and dry electrostatic precipitator (hot Cottrell), but the part of the "wet gas purification" various scrubber and wet electrostatic precipitator (mist Cottrell) It is included. In this part, to remove the dust in the gas from the roasting furnace, purpose is to obtain a clean SO2 gas. When arsenic and mercury in the raw material, is halogen and said substance is included, we can set up a dedicated removal equipment of each. Examples of the wet scrubber There are many things but, MECS, Inc. has focused on DynaWave.
Gas became clean enters the drying tower, it will remove absorb the H2O in the gas. From drying tower entrance is allowed to suck the air, and then the converter entrance of the O2 / SO2 ratio = ~ 1.2.
After this is basically does not change with the aforementioned sulfur combustion type, for gas passes through the purification system and the drying tower, the temperature has dropped to about 40 ℃, the catalytic reaction in the converter this optimal ~ 430 ℃ to cause the order to (usually the case of the catalyst) heated up, you can use the SO2 oxidation heat in the converter. Specifically, it is heated by causing the outlet gas and the heat exchange from the respective layers.
Absorption tower and Jogai-to after this is the same as the sulfur combustion.
For the conventional method, it is often becomes low SO2 concentrations in the converter inlet as compared to the sulfur combustion. Hence, the furnace recent metallurgical expression by suppressing the increase of the unreacted N2 components by using oxygenation air mixing oxygen into the combustion air, to lower the SO2 concentration, and those that do not increase the amount of gas It seems there are many. Such as in the case of sour gas from a conventional method and COG, it will not be able to raise the temperature of the gas entering the oxidation heat in too low, the converter. In this case, you need to'll supplemented with heat from outside continuously.
This, whether or not heat balance can take, you can be judged by the following formula.
Blower outlet (the first heat exchanger shell side inlet) gas sensible heat = Q1 Absorption tower entrance (the first heat exchanger tube side exit) gas heat = Q2 The SO2 → SO3 oxidation heat = Q3 in the converter
In
Q1 + Q3> Q2
Heat balance will take so long. However, because there is heat loss from the device surface of the converter system, in fact
(Q1 + Q3) * 0.9> Q2
It is safe if as a.
Other raw materials:
Clean flue gas desulfurization gas
PFD-4 please see. This is recovered from flue gas desulfurization equipment, such as Wellman Road Law, is the SO2 gas of high concentration in high purity (However, water vapor saturation). Since there is no need of gas purification, gas after removal of the H2O in the direct drying tower, will be sent to the converter. Because usually high SO2 concentration, you need to or use high-density catalyst or diluted with air. Exhaust of the absorption tower, so returned to the flue gas desulfurization gas, not necessarily the high conversion is required.
Dirty gas -1 (desulfurization sulfur waste liquid, waste sulfuric acid, containing H2S gas, etc.)
PFD-5 Please refer to. These raw materials, it is necessary to generate SO2 by first combustion. Because of course it combustion heat is generated, and the waste heat boiler is provided by a heat recovery in the form of steam. After that, it will remove the dust of gas was cooled and the gas at the gas purification equipment. After drying tower is the same as PFD-4, but the exhaust is released into the atmosphere after it was treated with a scrubber. Usually, because SO2 concentration is low, measures must be taken to reduce the H2O in the process gas.
Dirty Gas 2 (flue gas desulfurization gas containing dust)
PFD-6 Please refer to. This is because, as of activated coke law, those containing dust in the recovery SO2 gas, combustion furnace is not required gas purification equipment is necessary. Except there is no combustion furnace is the same apparatus sequence as a "dirty gas -1". However, because SO2 concentration is higher in the case of this gas, it will be rather necessary dilution with air.
Manufacturing process -4
Special process:
Wet method:
Whether the other raw materials any sulfur combustion, the catalytic reaction gas in the generic process is supplied to the converter does not contain H2O. This is to avoid the risk of equipment corrosion and stop time of the catalyst damage. The drying tower is used for the purpose, it has been absorbed and removed the H2O contained by washing the sulfur combustion air and process gas after the gas purification unit in the 93 ~ 95% H2SO4. However, there is also a process of contacting reaction while containing H2O in the gas. This is usually the gas in the beautiful but is also small equipment SO2 concentration is thin production volume, and the product will be only adopted in special conditions that may be a dilute sulfuric acid. Requires no drying tower as equipment, after the converter, the condenser and the cost of equipment and the electrical dust collector is only in place of the absorption tower is you can be kept low. However, because of that can not be concentrated sulfuric acid is that the application of the product is naturally limited, example that has now been adopted it seems that little.
WSA method:
A type of the above-mentioned wet method, but without causing total amount of condensed H2O in the gas, a method of obtaining a high concentration of sulfuric acid by partial condensation, Harudatopuso Inc. (Denmark) was developed in the mid 1980s. Gas containing H2O is oxidized SO2 is directly at the converter, the generated SO3 is a gaseous H2SO4 reacts with H2O. This H2SO4 vapor by partial condensation in a glass condenser to get the concentrated sulfuric acid. Oxidation heat generated by the converter will be recovered by the molten salt boiler. Concentrated sulfuric acid concentration of purification is determined by the H2O content in the gas. If 10% or less, Toka it possible to obtain 98% H2SO4. Moreover, by changing the SO3 Gasugu H2SO4 generated by converter, so remains SO3 concentration in the gas is always low, it means that same equilibrium with DC / DA method is shifted to the side to promote the oxidation of SO3, the final conversion Toka equal to or greater than 99%. Originally, the simple contact-type exhaust sulfuric equipment, such as boiler combustion gases, it was a process for producing sulfuric acid from a very thin SO2 concentration of the gas, at present, it and the high density SO2 from metallurgical type roasting furnace gas, H2S from oil refining, coke oven gas purification H2S, sulfur sludge, such as waste sulfuric acid and sulfuric acid drainage from the petrochemical, can accommodate a wide variety of raw materials, there is a construction track record 100 groups close to the world. In Japan, there was a facility from the petrochemical waste sulfuric acid, it is not currently for the generation process of the waste acid was discontinued. Globally, we have argued that already have a track record of more than 130 groups. (November 2014 currently) As compared with the general process, also in the plant cost, advantageous and manufacturers in the utility surface (Topuso Inc.) has claimed. However, in the molten sulfur raw materials, the original wet method because moisture is less in the air benefits I will think less. Also in the non-ferrous metal smelting, because the cost of the furnace and the gas purification part is greater than the sulfuric acid production facility, it will presumably cost benefit is small compared to other sulfur source. → WSA schematic flow→ experience in smelting gas Direction you are interested contact us please. Topuso's Japanese distributor, we will introduce the OTC.
SULFOX method:
those MECS, Inc. has developed, like the WSA method, it is wet sulfuric acid production process. It unique in this process, not only a thin SO2, is that it is a can produce sulfuric acid by oxidation in the converter within the catalyst also the H2S gas. Again by adjusting the condensing temperature? It obtained a high concentration of sulfuric acid, and then you have.
Non-stationary converter:
The catalyst of the converter is not divided into multiple stages, in a manner that switching between the entrance and exit of SO2 gas at regular time intervals, it is that you omit the converter around the gas heat exchanger. After preheating the catalyst, when you through the cold SO2 gas from the catalyst top, because among the first is the catalyst temperature oxidation start temperature or higher SO2 + 1 / 2O2 → SO3 Reaction of go, but you have cold gradually gas inlet side. If the gas inlet is now switch to from the catalyst bottom, the oxidation by touching the high temperature of the catalyst is continued, catalyst upper part which has been cold will be heated by the heat of reaction. If you have cold the bottom, now also conducts SO2 gas from the top ... If you continue this reaction sufficient conversion rate is obtained, thing.
It is a technology that has been developed in the former Soviet Union, there was operational cases until recent years in China. But the will not big final conversion rate is obtained, it is questionable whether really stable conversion rate can be maintained. In Japan there was a engineering company that sells this technology, but it does not have heard the story that was sold.
↧
Corrosion-resistant material for Sulfuric acid
Image may be NSFW.
Clik here to view.

Ceramic internal of an absorbing tower, Chiba, Japan
At the beginning :
Sulfuric acid facilities, is the fight against every day is corrosion and oxidation.
When you mistake the selection of material, it can not write leads to all stop of injury or equipment. Maximum attention is required.
Optimum recommended material at the current time of each device, " new facilities "and" equipment update in ", please refer Because it is stated for each device.
That want to keep in first remember corrosion by sulfuric acid,
For the metal material:
1. Corrosion by sulfuric acid, significantly different concentrations, temperature, dissolved components.
In the metal material, generally,"the amount of corrosion temperature increases 10 ℃ is two-fold,"It is said that. Since this is said to metal corrosion = chemical reaction of sulfuric acid and the metal, because the reaction rate is increased due to the rise of temperature.
There are no related at all relationship of concentration and the amount of corrosion. High concentration of sulfuric acid, it can not be said always to have strong corrosive.
Although strong lead = dilute sulfuric acid which are corroded rapidly to but no problem in practical use dilute sulfuric acid in carbon steel = room temperature in concentrated sulfuric acid resulting in soluble in concentrated sulfuric acid
In addition, it also varies in the dissolved components.
Sulfuric acid of sulfur combustion type, you may even those close to the dissolved impurities less purified sulfuric acid, but it is not said to be a "good because few impurities".
I, luxury nickel alloy circulating acid pump impeller, "even though not anything in the refining gas sulfuric acid plant, is severely corroded by sulfur burning sulfuric acid plant" was the experience of. That this is, during the refining gas is a very small amount, but that metals such as Cu, etc. have been dissolved NO2, these raw materials are beautiful too far sulfur to make a non-conductive coating, it could not be non-conductive coating but it has been estimated to cause.
So, "Examples of self-factory" will be greatly helpful, but "Examples of other plants" must not be to blindly reference.
If consult, let's strictly compared with the conditions of the factory conditions and their own factory.
2. Note the turbulence.
In particular, in the piping, you may site = elbow caused the flow of turbulence, cheese, corrosion downstream such as = valve seen violently. Especially often seen in stainless steel, these sites when a concern you should keep exchanged like Teflon lined.
3. Note that even material itself is changing.
With the advancement of technology, the material itself is improved in the constant component is changing subtly. Once upon a time was not a problem material also might cause problems now.
We do not talk about details because belonging to the know-how, when you update the process equipment using a stainless steel alloy, even though such should have been using the material "the same as the original", severe corrosion accident occurred.
When you try to study, has become very small compared to the original C (carbon) content of the new material, this was the cause of the corrosion.
JIS provisions of the C content of stainless steel, because there is only an upper limit, manufacturers I had been reduced more and more To the amount of C is, the "improvement for the service."
So, it is really "the same as the old days" thing of? And you do not have to change? Let's leave well to check the material manufacturer.
Inorganic materials (ceramics, glass, etc.) and organic synthetic resin:
These materials, when compared to metals, it is insensitive to changes in the concentration of sulfuric acid and temperature. If there is corrosion resistance in concentrated sulfuric acid, most things no problem even in dilute sulfuric acid.
However, for fuming sulfuric acid, Teflon and carbon it is not recommended.
For more details, it said in particulars.
References :
For documentation that summarizes the various corrosion-resistant material with sulfuric acid, it has settled well is old "sulfuric acid Handbook" is the best. (But it is out of print)
Other, there is also a book called "chemical equipment corrosion-resistant material table", which summarizes the corrosion-resistant material for various chemicals in addition to sulfuric acid. (This also has become out of print)
At present, materials such as corrosion curve of metal, probably most of the fastest way is to get the technical documentation is offered to manufacturers.
(Without permission, it had to publish anti-corrosion data to the net every manufacturers such as Mitsubishi Materials and Japan metallurgy, but no longer now. The reason is unknown.) * After this, we will continue to write the corrosion resistance and applications for each material.
Metal material:
"Metal material is corrosion with any time to varying degrees."
This also is true that I would like you to remember. It will not be long-lasting equipment to understand the "difference of degree."
Carbon steel :
SS Toka SGP in JIS, is a material that is expressed, such as the STPG.
The least expensive as the metal material, will that easy to come by.
Is this,
1) concentrated sulfuric acid 2) Same as above oleum 3 at room temperature (room temperature)) molten sulfur
There is practically sufficient corrosion resistance.
However, since the corrosion of certain parts of the flow will be greater than the stationary state, the use of the pipe is avoided, it should be used in the product storage tank.
(Room temperature of the piping SUS304 or 316, would be sure Teflon lining in high temperature of piping)
Other, but it has been used for the following sites, in the case of new construction and remodeling Let's say right.
(If economically afford)
A) converter around duct → converter is the first layer outlet duct SUS304
B) gas heat exchanger → tube and channel cover SUS304
C) combustion furnace and towers of the casing → SUS304
D) sulfur tank → ceiling SUS304 Stainless steel :
There are very many kinds, but I will in time in roughly SUS304 and 316 for sulfuric acid.
This of most applications
1) at room temperature of concentrated sulfuric acid, piping fuming sulfuric acid, pump, valve 2) converter around gas butterfly valve 3) molten sulfur valve It is. Other, there is also above A) ~ D) applications.
In addition 4) drying tower, absorption tower circulation acid piping
There is also in that factory used to, but since there is also a case that caused the trouble by being violently corrosion, as long as there is no past performance at the factory, is not recommended. Generally speaking, it is to have good when the low acid temperature.
Stainless steel, the temperature of the acid, the amount of impurities, the flow rate, can vary greatly, such as in the corrosion behavior presence or absence of flow of turbulence. In addition, it is also affected by the carbon content of the stainless steel itself. Performance of a factory, also necessarily fact that does not apply to other plants, it is a place well hear.
It is a special purpose, but the heat-resistant stainless steel such as SUS310S will be used in the boiler bypass gas valve in the sulfur burning.
High nickel alloys :
There are a wide variety of alloys for each manufacturer, but what is often used in sulfuric acid
1) Hastelloy-C group 2) Carpenter-20 (Alloy20)
3) pump manufacturer that has developed (such as Pilomet)
Below, we'll explain.
1) Hastelloy-C group
It is developed corrosion-resistant alloy of the United States Haynes International Inc.. Although initially it was Tadano "C",
Then various kinds have been developed.
The is often used in concentrated sulfuric acid C276
C22
It is two.
(In Haynes's home page is located that there is a corrosion resistance to "B3" because sulfuric acid, but this is the original as for anti-HCl)
C276:
Components
Ni 57, Cr 14.5-16.5, Mo 15.0-17.0, W 3-4.5, Fe 4.0-7.0, Co≤2.5, Si≤0.08, Mn≤1.0, C≤0.01, V≤0.35
It is widely used in the plate cooler for the tower circulation acid.
According to our catalog Haynes "by preventing particle deposition in the weld heating section, and has a high degree of corrosion resistance without treatment after welding""and localized corrosion, and there is an oxidizing, resistant to reducing substances."→ Haynes catalog C276 → corrosion curve of C276
Just "metal material is corrosion with any time to varying degrees," he said. C276 is no exception. In the plate cooler, the entrance of San is corrosion most early (because the temperature is the highest).
Therefore, after you have used a few years, you need to check is opened.
Also this time, also help to extend the life of the entire cooler to the entrance and exit of the acid in reverse. → " maintenance "," acid cooler "
C22:
Components
Ni 56, Cr 22, Mo 13, W 35, Fe 3, Co≤2.5, Si≤0.08, Mn≤0.50, C≤0.010, V≤0.35
This also seems to be used to the plate cooler.
In the catalogs of Haynes, "especially" C276 has excellent corrosion resistance than "pitting, crevice corrosion, you have stated that there is strong resistance to stress corrosion cracking", concentration for sulfuric acid in the same catalog - temperature - corrosion amount Look at the graph and, but should not be seen as there is much difference in the 98% H2SO4. →
2)Carpenter-20 (Alloy 20)
It has been developed by the United States Carpenter Technologies Corp., component Ni 34, Cr 20, Mo 2.5, Cu3.5, Fe balance, Nb≤1 (≥C * 8), Si≤1, Mn≤2, C≤ 0.06
Hastelloy-C22 as well as has been touted as "pitting, crevice corrosion, resistant to stress corrosion cracking" but it seems to the extent that is now being used in wire mesh demister of the tower exit.
3) pump manufacturer that has developed (such as Pilomet)
Ltd. Matsuda pump Works of Pilomet, such as Lewmet of rice Lewis is something that has been developed as a material for sulfuric acid pump.
However, even these, you must be careful because you may be subject to corrosion by the "impurities" of temperature, other than the sulfate concentration.
Tantalum :
Tantalum, 100 ℃ almost completely in the following concentrated sulfuric acid (corrosion weight = 0) is shown a corrosion resistance, shows no practical problem corrosion resistance at 200 ℃ or less.
However, for very expensive, it has been used parts that are used special a small amount, for example, the diaphragm of the diaphragm type pressure liquid to a sulfuric acid plant.
Also by heating concentrated dilute sulfuric acid is used as a lining material in concentrated cans in equipment for the production of concentrated sulfuric acid.
However, the fuming sulfuric acid it must be careful because it is corrosion even at low temperatures.
Cast iron :
Selfish, cast iron had been widely used as piping material and material of acid pump for concentrated sulfuric acid.
(Fuming sulfuric acid, next to SiO2 is silicon content in the cast iron oxidation, this can not be used because that would divide the material itself swells)
The low temperature of concentrated sulfuric acid at a low cost and has in its own way, but in cast iron distinctive of "su" problem, one day you suddenly or cause a sulfuric acid leak accident.
Production of cast iron, so typical 3K is the work, has been migrated production from early to subcontract overseas, seems to have become the maintenance of quality it is also difficult.
As for the concentrated sulfuric acid, and high-silicon cast iron containing around 15% Si, there was a low chromium cast iron containing 1% less than the Cr, almost all stainless steels and high nickel alloys currently are alternative such as Teflon lining You.
High silicon cast iron, seems to the electrode of current even electrolysis equipment being used.
Lead :
Lead is also a material that has been widely used in the nitric acid-type era sulfuric acid.
The dilute sulfuric acid there is corrosion resistance, but it can not be used because it soluble in concentrated sulfuric acid.
Even in contact sulfuric acid, although in dilute sulfuric acid portion of gas purification equipment other than sulfur raw materials (such as the casing of mist Cottrell) was used, this was also replaced by the FRP and other organic material. Again and price, it seems that is a problem that the weight is increased.
By decreased demand, craftsman itself to work also declined. Lead, because there is a use as a shielding material of nuclear power plants in other than sulfuric acid plant, there in is like Some craftsman in its own way, under the influence of this accident, I will also decrease.
It had been also hard lead with increased hardness by the addition of 3-12% of antimony in the lead used in such dispersion tube of pump and cooling tower, which was also no longer mostly seen now.
Lead, the hardness lead both, it is now replaced by the plastics and ceramics such as Teflon and PP.
Other metals:
In other metals, gold, platinum is about to have a sufficient corrosion resistance to concentrated sulfuric acid.
Platinum, seems to have been used as a spray of dilute sulfuric acid in the nitric acid-type equipment such as lead room selfishness. (It is sometimes so stolen)
Other metals, it can safely keep in stores almost all the "unavailable" for the concentrated sulfuric acid.
For the dilute sulfuric acid, titanium, zirconium seems there is also some of the corrosion resistance, etc., but does not have expensive late almost used.
Inorganic materials :
Acid porcelain :
Acid porcelain, lining material and sites that is in direct contact with the sulfuric acid, such as towers and pump tank as brick, has been used to tower packings such as interface Rochus saddle.
The component basis, is what good be considered the same as porcelain for tableware (such as Arita). Come to think of it, is a leading manufacturer of acid porcelain Iwaojikikogyo Co., Ltd. is located in Arita. Originally, it seems to be a ceramics manufacturers such as tableware.
Concentrated sulfuric acid, there is a nearly complete corrosion resistance in dilute sulfuric acid. In my experience, acid brick that was used 50 Toshi-yo also, apparently no different at all new.
Recently, domestic to that of the quality of the clay has been reduced, it seems to have fallen somewhat from those quality-old. The color of the bricks, was a complete white things of long ago, those of recently has been tinged with pale reddish brown. I will be thought that due to the impurities.
Brick is possible semi-permanent use, but the joint material to be used during construction will be affected in the sulfuric acid. Around from the gap of the joint material in the back of the sulfuric acid is brick, the casing is damaged by corrosion of the carbon steel of the casing. To prevent this, in recent years it has been made to put a Teflon sheet between the bricks and the casing.
→ "equipment update,"" drying tower, absorption tower "reference
As the standard of acid porcelain, following JIS, and Iwaojikikogyo Ltd. Please refer to the catalog.
JIS R1501 general General Rules of the chemical industry for the oxidation porcelain
JIS R1503 test methods for the chemical industry acid porcelain
JIS R1528 for the chemical industry acid porcelain fillings
JIS R1536 for the chemical industry acid heat-resistant bricks
The oxidation porcelain manufacturer, NGK Insulators, Ltd. is also available.
In addition, you heard that in recent years has been around also made in China acid brick, I have never used still.
Glass :
Glass also, dilute sulfuric acid, there is a nearly complete corrosion resistance in both of concentrated sulfuric acid. (Especially in the case of hard glass = borosilicate glass)
However, since weak fragile to shock, it is rare to be used as such.
Those of the wall thickness is used for sight glass in the middle of the piping.
Also, heat-resistant glass which has improved thermal shock resistance by lowering the thermal expansion coefficient, is used for the absorption tower for purification of concentrated sulfuric acid production. This, Corning Pyrex is famous.
However, because it is expensive, recently it has been replaced by glass-lined below.
Glass lining (GL):
Glass cast iron, by lining the inside of carbon steel or stainless steel, is what was to maintain the mechanical strength and corrosion resistance.
If the pipe is inserted into the metal pipe after heating the glass tube, to those brought into close contact by applying pressure from the inside, while others baked covered with a glaze vitreous inside of the metal tube.
Prepared by the course of the latter method in such a large container. This will things to be rather referred to as "enamel".
Concentrated sulfuric acid corrosion resistance, of course, since it helps to minimize pollution of sulfuric acid by the dissolution of the metal, which is used in the purification of concentrated sulfuric acid manufacturing equipment instead of quartz glass.
In the case of printing method, since it may rarely a pinhole, you must perform a sure pin hole test at the time of completion.
In addition, it said that the excellent mechanical strength, because there is a risk of peeling is give and blow lining glassy, such blow is taboo.
And such as suddenly put the high temperature of the liquid, care must be taken because there is that glass is peeled off by thermal shock.
As those of similar applications, there is a Teflon lining, but more of the glass lining is excellent in heat resistance, it is used in higher temperature applications. It Would not it be okay to the boiling point.
For other chemicals sulfuric acid, weak alkali because it is glass, also violently it is affected because the phosphoric acid in the fluorine is difficult to use. It is also affected to a high temperature of steam.
Currently, for to alkali, so it seems there is also a special case, such as for a pair of steam please try to consult with the manufacturer.
As a manufacturer, there is a following.
Ltd. Kobelco Eco-Solutions
NGK Insulators Ltd.
Hakkosangyo Co., Ltd.
AGC Technology Solutions Co., Ltd. - insertable GL piping only Fire-stone :
This is a kind of pumice that lava was Deki solidified, those of Niijima production of Izu Islands have been conventionally used.
Lightly (specific gravity 1.2-1.4), because there are easy and acid resistance processing, it will be used in gas purification part in equipment other than sulfur combustion.
In applications other than sulfuric acid, since it also has excellent fire resistance, it is used as the acid lining material of the chimney. It is also used as a general of residential building materials.
As manufacturers and contractors, anti-fire stone Industry Co., Ltd., has Niijima Bussan Co., Ltd..
Organic material :
Teflon :
Originally with Teflon, it is that of PTFE that DuPont has developed in 1938.
PTFE = polytetrafluoroethylene (-CF2-CF2-) n
It has high chemical resistance, heat resistance, and is also has excellent properties such as low coefficient of friction, a part of the F in order to improve this because of the poor workability hydrogen, chlorine, other which was replaced by the olefin has been developed. Collectively, these are called "fluorine resin".
FEP = tetrafluoroethylene-hexafluoropropylene copolymer (-CF2-CF2-) n - (- CF2-C2F4-) m
ETFE = tetrafluoroethylene-ethylene copolymer (-CF2-CF2-) n - (- CH2-CH2-) m
PFA = tetrafluoroethylene-perfluoroalkyl vinyl ether copolymer (-CF2-CF2-) n - (- CF2-CF2OCF3-) m
PVDF = polyvinylidene fluoride (-CF2-CH2-) n
In DuPont, it will be referred to PTFE, PFA, FEP, the "Teflon", but other fluorine resin are wearing each different name, in Japan we practice called everyone "Teflon".
Although as a concentrated sulfuric acid and all organic materials in the best, without being corroded with time differences between the metal, without also contaminating the sulfuric acid by dissolution of the components, it is an ideal material.
However, other than PTFE and PFA has difficulty in heat resistance, and can not be used in oleum for transmitting the SO3.
As a lining material of many metal inner face, piping, it is used valve, such as a vessel.
As a lining material of the valve, NICHIAS Co., Ltd. is a PFA, Valqua Industries Co., Ltd. is I am using PTFE and PFA.
In addition, as a thin tube acid cooler it is used to.
When used as a gasket, the left but it will be used, flexible pinch cushioning material such as rubber in order to increase, also it has to not mix a filler of mineral in order to avoid cold flow.
Drying tower, absorption tower, and such as a pump tank for them, in towers and vessels lining the acid brick, the corrosion due to the fact that touch is across the sheet directly to the (seat lining) shell sulfuric acid between the brick and steel shell It has been made to prevent. However, Teflon because it does not adhere to brick in steel, you can paste it or use the process the surface or adhesive.
From the characteristic that it does not contaminate the product, purified sulfuric acid, has been often used for high-purity sulfuric acid.
The nature of the typical Teflon class I is shown below.
Image may be NSFW.
Clik here to view.
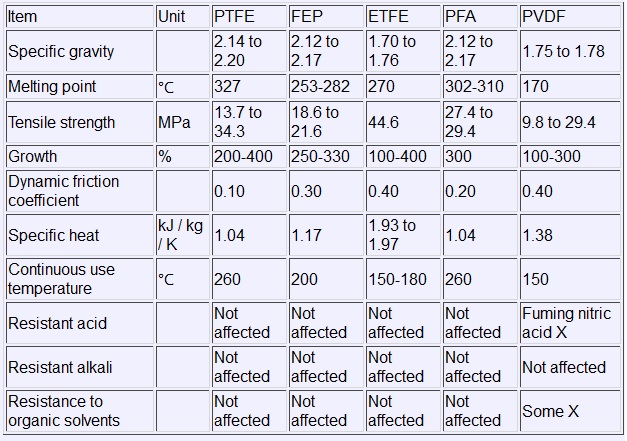
Viton :
Viton is the same fluorine rubber DuPont has developed a Teflon.
Compared to teflon, flexible, on rich in elasticity, strong acids include concentrated sulfuric acid, withstand strong alkali, excellent heat resistance (~ 250 ℃), the nature of Teflon as oil resistance, excellent in solvent resistance It also features.
Structurally, the base is what is obtained by copolymerizing hexafluoropropylene in polyvinylidene fluoride.
(-CF2-CH2-) n - (- CF2-C2F4-) m
Currently, there are those obtained by copolymerizingother tetrafluoroethylene and perfluoroalkyl vinyl ether according to the application.
In the sulfuric acid plant, it is common as a gasket of concentrated sulfuric acid for the plate cooler.
FRP :
FRP stands for Fiber Reinforced Plastics.
Because it is sometimes referred to as "fiber reinforced plastic", although it is considered that the combination of a wide variety, as being practical use,
Plastic = unsaturated polyester resins, epoxy resins, polyamides, polymethyl methacrylate fiber = glass fiber, carbon fiber, aramid fiber (Kevlar)
And so on.
Lighter than the metal, there also have strength and excellent corrosion resistance, but it will not be able to withstand it will be carbonized in concentrated sulfuric acid.
Only, it is intended to be used in an atmosphere of dilute sulfuric acid and wet SO2 gas. Washing tower, mist Cottrell of the casing, it will be used, such as the gas duct of the gas purification system.
Is it been put to practical use in sulfuric acid facilities,
Unsaturated polyester resin + glass fiber
It is a combination of.
There is a kind also in unsaturated polyester, isophthalic acid-based, bisphenol-based, there is a vinyl ester. 2 who has excellent corrosion resistance as compared to the isophthalic acid system later, it seems no problem in isophthalic acid system for the sulfuric acid plant.
If you want to use in gas purification system, in the conditions, including fluorine in the gas, because there is a danger that glass fiber is corroded, and synthetic resins such as PP as the fibers on the surface in contact with the gas, you can use the carbon fiber.
As a manufacturer, in the major
Showa Denko Co., Ltd.
Oriental Gas Kiko Co., Ltd.
Fuji Resin Industry Co., Ltd.
There is such, but since that can be anyone production if there is a resin and glass fiber, to say that small and medium-sized manufacturers is infinite number is not an exaggeration.
PVC (polyvinyl chloride):
It is one that is used in large quantities is referred to as a "PVC".
FRP Again, it can not be used will be carbonized in concentrated sulfuric acid. Is for the dilute sulfuric acid it is possible to use.
However, it is degraded by ultraviolet light, so easy to crack in the piping of the outdoors will require regular updates.
For reinforcement, which was inserted PVC in the carbon steel pipe (LP tube), while others that were plated FRP on the outside of the PVC pipe.
PVC, because it contains chlorine, from concern to generate dioxin when incinerated, seems to have been reduced use.
PE (polyethylene):
This also is what is used in large quantities as plastics.
There are HDPE and LDPE but, HDPE (high density polyethylene) made of tank and pipes are used in the sulfuric acid plant.
PE, although at high temperatures will be attacked by concentrated sulfuric acid, there is no problem in practical use at room temperature.
Therefore, the storage tank of purified sulfuric acid and, it has been used as a 20L plastic tank for the product sulfuric acid sales.
The polyethylene tank, Dairaito Ltd. is famous ones.
Those lining the PE to carbon steel piping, have been used to dilute sulfuric acid. Even for concentrated sulfuric acid, I think that it can be used as long as it is a low temperature.
PP (polypropylene):
Also PP should say representative also of thermoplastic resin along with the PE, has been put to practical use as a piping material, it seems to have become the alternative of PVC pipe.
This is also used to dilute sulfuric acid is possible, concentrated sulfuric acid, it can not be especially used in high temperature.
Rubber :
Natural rubber even though the rubber, there are synthetic rubber various Although it is a wide variety, corrosion resistance is generally to sulfuric acid "It is attacked by concentrated sulfuric acid, withstand the dilute sulfuric acid."
It is. ( Viton I except = fluorine rubber)
Therefore, it is hardly used for the sulfuric acid plant of sulfur raw materials, and are used in gas purification equipment by other raw materials. Majority is used as a lining material of carbon steel.
Carbon :
It is referred to as "carbon", but one that is improved is by impregnating synthetic resin in the synthetic graphite strength and air-tightness those used in the sulfuric acid plant, properly to be referred to as "impervious graphite" It is.
Phenol resin is common as a resin, but some impregnated with Teflon.
Heat transfer is very good, the dilute sulfuric acid there is a sufficient corrosion resistance, but it is attacked violently by generating CO2 in hot concentrated sulfuric acid. Therefore,
1) cooler 2 of sulfuric acid dilution equipment) and is used to dilute sulfuric acid cooler and gas cooler of gas purification equipment.
It used if concentrated sulfuric acid of 90 ℃ about the absorption tower outlet but should of possible, increased concentration of product sulfuric acid is abnormally in tourists operation mistake when it was used as a selfish product acid cooler, Become a fuming sulfuric acid Have closed, this time there was an accident that the entire cooler melts. Since there is such a thing, it is not recommended to concentrated sulfuric acid cooler.
As the heat exchanger for the sulfuric acid plant, it is often for shell / tube type that is easy to clean the scale, but as the heat exchanger will have this also in addition to the block type or plate type.
As a manufacturer, therefore expensive electricity rates, which account for large proportion of the cost, Japan independent manufacturers no longer. Both currently is a joint venture with overseas manufacturers.
Nippon Carbon Melthene (Ltd.) = Japan (Nippon Carbon) + France (Melthene)
Graphite Chemical Co., Ltd. = Japan (Tokai Carbon) + US (SGL)
And so on.
↧
Sulfuric Acid Plant Calculation
Calculation:
1) concentrated sulfuric acid (98.3% H2SO4) was diluted with water, Calculate the amount of water when making 62.5% H2SO4.
At the time of diluted sulfuric acid temperature :
2) in the case of the above example, Calculate the temperature of the product 62.5% sulfuric acid. 98.3% sulfuric acid is 40 ℃, the water I and 25 ℃.
During the operation management of the sulfuric acid plant, or you need a huge amount of computational work at the time of new construction and renovation of facilities. Here I am not going to describe all of them.Of sulfuric acid dilution water :
Please refer to a relatively opportunities are many, and so a brief description of some for a useful calculation.
- Dilution during the amount of water in the sulfuric acid
- Ditto acid temperature
- Heat loss from the equipment
- Emissions possible SOx amount (K value regulation)
- Etc.
1) concentrated sulfuric acid (98.3% H2SO4) was diluted with water, Calculate the amount of water when making 62.5% H2SO4.
Traditionally, for each amount of sulfuric acid for obtaining a concentration of the target by mixing different concentrations of sulfuric acid, a convenient method of "square law" is famous.
This is, each of sulfuric acid concentration A% before mixing and B%, and a sulfuric acid concentration C% of the target place as described below, and the subtraction in an oblique direction, respectively.
A C - B C B A - C
As a result, (CB) :( AC) = concentration A% of the amount of sulfuric acid: It becomes the concentration B% of the amount of sulfuric acid.
For example, 98% H2SO4 (A) and 20% H2SO4 (B) are mixed with 94% H2SO4 when making the (C) is
CB = 94-20 = 74 AC = 98-94 = 4
In other words, it is the result that should I you mixed the 98% sulfuric acid = 74 parts and 20% sulfuric acid = 4 parts.
Therefore, the solution of the question
98.3 62.5 62.5 0 35.8
To 98.3% 62.5 parts of sulfuric acid, and it will may be added 35.8 parts of water (57.8% of concentrated sulfuric acid).
* In the case of mixing of fuming sulfuric acid are each displayed in all SO3 amount, and then apply the rectangle method in the same manner.
For example, "a mixture of fuming sulfuric acid and 94% sulfuric acid of 25% free-SO3, 98% get a sulfuric acid" case:
86.22 3.27 80.0 76.73 6.22
∴25% freeSO3 fuming sulfuric acid: 94% sulfuric acid = 3.27: 6.22 I will be mixed in a ratio of.
At the time of diluted sulfuric acid temperature :
2) in the case of the above example, Calculate the temperature of the product 62.5% sulfuric acid. 98.3% sulfuric acid is 40 ℃, the water I and 25 ℃.
This is First, you must calculate the heat of dilution of sulfuric acid. There are several ways, engineering sulfuric acid (moat, Nakagawa AD, Inc., 1967) According to the,
If you want to dilute the H2SO4 of 1 mol of water n mol, the dilution heat
Q = 17860n / (n + 1.7983) ··· (1)
Q: cal / mol-H2SO4 n: mol-H2O / mol-H2SO4
When generation to the sulfuric acid concentration = 100A%
A = 98.08 / (18.02n + 98.08) Therefore, n = (98.08 / 18.02) (1 / A-1)
When you assign this to the equation (1)
Q = 97209 (1-A) / (5.4428 -3.6445A)
Therefore, 100% H2SO4 → 98.3% H2SO4 dilution heat of: Q1 = 97209 * (1-0.983) / (5.4428 -3.6445 * 0.983) = 888cal / mol-H2SO4
100% H2SO4 → 62.5% H2SO4 dilution heat of: Q2 = 97209 * (1-0.625) / (5.4428 -3.6445 * 0.625) = 11,518cal / mol-H2SO4
∴98.3% H2SO4 → 62.5% H2SO4 of dilution heat ΔQ = Q2 - Q1 = 10,630cal / mol-H2SO4 = 108 kcal / kg-H2SO4
98.3% When will the amount of the sulfuric acid and 1kg, Heat of dilution Hd = 108 * 0.983 = 106kcal
98.3% held by the sensible heat of sulfuric acid H1 = 0.344 * 1 * 40 = 14 kcal Water holding sensible heat H2 = 1 * 0.578 * 25 = 14 kcal
∴ held sensible heat of the generated 62.5% sulfuric acid H3 = 106 + 14 + 14 = 134kcal Assuming this temperature and 120 ℃, specific heat = 0.553kca / kg / ℃, generating 62.5% sulfuric acid = 1.578kg so
Generated 62.5% sulfuric acid temperature = 134 / 1.578 / 0.553 = 153 ℃
Boiling point of 62.5% H2SO4 is so 145 ℃, it will be sulfuric acid boil. In such a case, and to cool the sulfuric acid immediately after mixing in a shell-and-tube cooler, it will be that the heat exchange is hindered because of the bubble of steam in the tube, and diluted and cooling is divided into two stages How it is taken.→ "Various sulfuric acid production process", "dilute sulfuric acid See "
For example, * first stage 98.3% → 80% * The second stage 80% → 62.5%
As a method of calculating the heat of dilution, there is also a way to use a chart of Othmer and Fusullo et al. Numerical value of the data to be used is different in each subtle, practically no problem. (Of course, such as the heat transfer area of cooler you should look at a sufficient margin)
↧
↧
Sulfuric Acid Trouble cases
1.SO3 white smoke jet accident
October 1992, from the factory length of the Malaysian company many years of relationship, we have received a sudden international telephone.2.Impeller melts!
"Help, Ono san!"
At the time of re-start after the regular repair, and will start-up and operation of the sulfur while stopping the circulation pump of the absorption tower, a large amount of SO3 unabsorbed is ejected from the chimney, the adjacent competitors factory (for export flows into was a clothing manufacturer), a large number of employees, most of them fell a young woman is difficulty breathing, Toka he was a great uproar in the national news. Of course, sulfuric acid plant is shut down indefinitely.
Why? After absorption tower circulation pump has not stopped, it would not move combustion air blower? And when I heard the reason, "because the periodic maintenance that while releasing the interlock, had forgotten to return to the original" thing with.
It is a simple mistake To hear. However, the result is serious.
"From the DOE (Department of environment, Ministry of the Environment), until it receives a complete preventive measures are said not to resume operations, it can not be trusted even out the proposed measures, since you are an expert of the plant maker DOE and because also would be convinced, and I say that just to me to make the proposed measures to come. "
Director, because it was the president with even people missed, the next day to discuss the correspondence, it was that I'll go anyway.
With that as soon take the airplane ticket, I went to the local 3 days after the phone call.
Customer and consultation in the field, to make the idea of "also came a large amount of SOx newly established capable of absorbing scrubber after absorption tower", PFD, Process description, Construction schedule other, it has created a DOE submitted documents in the field.
We came back in the stay of 10 days. In subsequent information, DOE is Toka he is convinced in my Report, who admitted operations resume. (When you think from now, you will of much use also Under the table)
Lessons learned: In developing countries, even in the safety device, because sometimes resulting in a start while the removed, by the going.
(Even if I say that, it takes the measures to the bottom and plant cost will be enormous, and this will become a competitive disadvantage. It is a place to some extent it may not forced referred to as a "no choice". Difficult)
This is a construction completion and operation beginning of the trouble of sulfuric acid plant overseas.3.Unexpected unexpected to "sulfur by-product of "
Because the DC / DA method, drying tower, intermediate absorption tower, and the final absorption tower, but I tower are arranged 3 groups, among drying tower and the first absorption tower that, in particular impeller of drying tower of the pump, nearly 45 It is from being gone clean melt in the day.
Studio is a long-established chemical pump manufacturer in Japan, is particularly company in the circulation pump for the sulfuric acid, which boasts Japan's track record. The material of the impeller that has been used is one that manufacturers have been developed purposely as "a sulfate plant circulation pump", previously it is of being used more than two years at large facilities in Japan and overseas.
However, anyway it sends the spare parts, it is no longer is also melted, while repeating the feed for the next ... and gave a corrosion test of the pump impeller for material just to make sure the manufacturer's lab.
The result is over without a problem. Manufacturer name is "than there is this customer-specific special circumstances?".
Suddenly it Omoitachi, "there is a track record for more than two years," the place where I had taught a third of operating conditions that, either, exhaust gas of copper smelting was the raw material. However, the raw material of the plant that caused the trouble, is recovering molten sulfur from petroleum.
"Than sulfuric acid is too beautiful?"
"There is no such a thing, I just paid the same pump also in the country P, Inc."
P company, has to do with my company, also know well technician. the phone to talk I was at the circumstances "recently to think of it, since the current value of the pump motor is down, plan is to check with close temporary stop" is called.
Question to visit the open day, where I had to show an impeller, full of holes by corrosion, state that seen through the other side.
"It was dangerous!"
Manufacturer of salespeople, and cause differences of raw materials, it was admitted at last.
When sulfur is of raw materials, product sulfuric acid is a very clean, is enough to pass the purification of sulfuric acid standard. The stainless steel-based alloys, it is likely that corrosion resistance is imparted by the non-conductive film is formed on the surface by oxidizing ions in the sulfuric acid, but this non-conductive film produced in (very little of the impurities) sulfuric acid clean It will be considered are not. (Smelting gas sulfuric acid, is considered a NOx generated in trace amounts of dust and electrostatic precipitator pole becomes the oxidizing ions)
Trouble is, no longer keep up with the supply to the exchange of frequent spare impeller manufacturer, place that supplied the impeller "for dilute sulfuric acid" with the intention of "band-aid", it can be seen that this is long-lasting, it has been resolved at last. It was a great achievement of the injury.
Lessons learned:
1."Examples of other companies" is not necessarily true for the corrosion of sulfuric acid.
2."Clean sulfuric acid" is, in the stainless steel-based material is corrosive.
This is a by-product from the coke oven gas of certain steel mills of China, is the trouble with sulfuric acid plant as a raw material to sour gas that contains H2S.4.Carbon steel cooling tower parts of the delivery time
In addition to the H2S in the sour gas, CH4, C2H6, C6H6, CS2, contains miscellaneous gas of ammonia ... and so on. By burning them in a furnace SO2, H2O, cooled to from the CO2, N2, and sends it after the wet dust collector into the drying tower.
Equipment of commissioning is also complete, it is plant start finally.
The flowing air, and ignited in sour gas, but was gradually ... will Yuku raise the combustion furnace exit gas temperature by adjusting the gas / air ratio, does not increase the gas temperature is quite. SO2 concentration also remains low. In was considered "because the amount of air is too much for the amount of gas, combustion gas temperature does not rise is dilution", I was squeezing the air. However, the temperature also SO2 concentration does not increase. I Yuki down rather.
"Do sour gas concentration is low for?""Whether nitrogen is too much?"
Etc., and examine various but I do not know. In the meantime, the site received a report with the "cooling tower circulating liquid is cloudy" from engineers who had been patrol, and I come to the site.
Certainly, it has liquid is cloudy. What would? And, when you look good well, it looks fine particles of sulfur.
I noticed the "Oh!".
The combustion furnace exit gas temperature does not increase, not because the air is too much, it was because air rather was insufficient. Therefore, look combustion H2S gas is conducted to the cooling tower, where Claus reaction 2H2S + SO2 → 3S + 2H2O
The causes, are you sulfur is deposited.
(Flow meters of sour gas and air had been attached, because the composition of the gas is uncertain, accurate flow rate ratio of the raw material gas and air do not know)
Immediately stop the operation, and inspect, by-product sulfur, past the cooling tower, has been deposited on the collecting electrode of mist Cottrell, the electrode plate was covered in thick sulfur of smack yellow .
Then round three days, still cold Shanghai of March, we clean the Cottrell inside of sulfur using the water in the colleagues and two people.
I was was before delivery of the plant, Chinese and Japan of the original 請会 company also chilly as the "idea of you mistake", I did not get to help out at all.
As lessons learned from this accident, in subsequent similar sulfuric acid plant, gas analyzer after leaving the furnace,it was decided toalso be sure to install O2 gauge not only the SO2 meter.If the attached O2 meter, it is "O2 = 0%" or "air is not enough!" And because it should have found immediately.
5.Chemical injury accident
In the country of new equipment, raw material gas includes a halogen, it was decided to use a Teflon impregnated carbon steel superficial to the first gas cooling tower.
From performance and price, but I decided to import the made in France, after the arrival in Japan, and received contact from the Japanese branch of manufacturers and "has cracked the gas inlet nozzle".
Of course, we should not and not replaced. If you say case replacement immediately, "We said that it take five months," the manufacturer says with.
Not a joke, there are only three months until the operation of the equipment."Is it not somehow in a month?""Try Kakea~tsu and France"
Since the branch office of humans are Japanese, (because it is France 8 hours late, night) in the early morning every day and will demand the payment by phone to the local factory addressed, Lachi does not fall.
From the customer, "You, Once hit the ass in Tomarikon to the manufacturer's factory?" But was told and the sarcasm, just immediately after the 9.11 terrorist attacks, overseas business trip the era of self-restraint. It does not take.
"Because pay three times the nozzle price, is not you? Expedited delivery" was also offer a.
To them "from the local plant manager," the employee had a contact with the "no longer stomach 2 months near at all vacation. Even got much money, you can not work if there are no employees"
I'll say that. You see, vacation! Vacation is a top priority of the French. Japanese would Komaro, but bankruptcy used by Americans anyway.
I've decided to prepared to pay the penalty, a blessing in disguise, if trouble occurs in the construction of the upstream of the desulfurization equipment, the construction period was delayed more than six months. Thanks, we have achieved somehow exchange of nozzle before commissioning.
It was a good study. Later, I "made in France of the machine, only buy Na when a delivery room," the men had commanded. Come to think of it, there was a local trading company of the president of Malaysia of the relationship a long time ago, "I am, no matter how you do not buy is made in France and the Italian-made products even cheaper," he had said. The reason is, that the delivery time of the because bullshit. America is also quite irresponsible, United Kingdom Well Well, can most credit or "but Japan and Germany."
After a great deal, we have imported a special machine from France for the plant of pharmaceutical products. Because it was customer's specified by the manufacturer. But this is totally no problem. By companies that are in the Alsace region, it is a Germany-based and from the name. Alsace is historically land that France and Germany have been repeating the territorial dispute. I was thinking like "kana because that contains the blood of the Germans."
Concentrated sulfuric acid, and damage to the human body, can cause severe burns. After healing also, it will remain ugly keloid-like traces.6."developing countries work in. "
Also my body, the side of the upper arm and the navel, there are burn marks. Both, is the wounds received in Nigeria.
This such as lighter, my cousin when I was a junior high school student, was killed instantly in an accident that wear a sulfuric acid from the head. In Bangladesh, my place of work to be in operation guidance, tank exploded in a welding spark, local people 5 people was also an accident that death.
In Nigeria, also one of the bank's Japanese supervisor was injured quite a large amount, it has been forced to hospital for a while. This is, if you are working to remove the piping of sulfuric acid together with local people, to have still contains sulfuric acid inside by mistake as "empty", with sulfuric acid which is blowing in order to loosen the bolts of the flange It is the thing which was injured. Moreover, "the flange bolts, be loosened from the opposite side of the body,""Even in the sky, in going in that are filled sulfuric acid inside" that, did not observe that you are taught in safety education .
Concentrated sulfuric acid, because it itself is dangerous, equipment it should be structure and material that does not go out and leak easily. In the past, it did not get in quite such measures for economic reasons, because the current to enter the equipment is hand inexpensive of good material, it is safe when compared to the old days.
To prevent the accident? Over facilities, it should be all "Fool-proof". This is a good word, "fool even okay", in other words, so as not to cause an accident even if the erroneous operation, or it is to design the equipment so that not occur erroneous operation.
From behavioral, it is never "that you do not neglect the principle." Also in the above Nigeria of accident, that it had ignored the note and procedures that are taught in safety education was the cause of the accident.
Eteshite human beings, is what they want to omit the procedure according to get used to. If you have cut corners to say is "troublesome because,""since the accident until now has not happened once," accident only when such is the one that occurs.
And, for the time that had happened Should acid leakage, it is to keep the proper protective equipment and sufficient number secure.
Everyone, is a matter of course. Yes, accidents happen because not doing commonplace things commonplace. When the nuclear accident in Fukushima, and never will be so much serious and did not imagine. Since TEPCO is a leading company, because I thought that the safety procedures also training also be sufficiently.
However, even pump that cools the ② furnace did not imagine tsunami of ①20m, is located in the place also power supply is low, has become unusable everyone in the tsunami (backup was not secured in a safe place) ③ " etc. of blunder corresponding manual was not about the situation in which cooling water is stopped Maru "in the tsunami is now clearly one after another. Large companies also do not take credit.
Everyone, in the accident, to a painful eye is yours. Please do not compromise in regard safety.
Domestic as well, and it has worked in the "developing countries" overseas.7.Of gas heat exchanger high temperature corrosion
The secret to achieve the work vigorously?→ is "patience". Never angry Do not be. Here's not in Japan, because the opponent's not a Japanese. (In other words, "common sense" of Japan, in developing countries's the "insane")
In Malaysia, concrete sulfur pits, underground water has been entering the molten sulfur from the beginning full of cracks. Since the temperature of sulfur is also 150 ℃, of course water boils, it becomes steam. and "It's a hot spring, like," I was laughing with.
It is because you are using a "cold a minus to cement" = moisture absorption to defective cement that became bad of coagulation. We want to focus on cost than quality. Cheap thing only is not ready, after the "on-site white somehow."
And I did not want Yari because the corrosion, but we cover all of the inner surface of the concrete layer in steel plate. And then, now Rashiku sloppy welding, steam has spouting along the weld line.
After I complain to the contractor, "In so cheap contract, very welder and I do not hire something of qualified personnel" We Usobui with.
The fact that? I'm allowed to welding work on amateur unqualified!
Local construction work is the customer's jurisdiction. Apparently, construction managers of the customer are, they apparently have put bosom by kickback the contract money. But when you hear, in Malaysia it Toka's what "the scope of common sense."
This, rampant of kickback or bribe, so common in developing countries. In Nigeria, it was called a "dash" to a bribe to pass to the police officers and officials. Even doodling To when to end whether bureaucracy you do not know, dash if I get even gold, or What a sense that it is sudden acceleration?
Poor maintenance of infrastructure is also common.
In Nigeria, anyway power failure occurs frequently, but was also construction commissioning was hard.
Sulfuric acid facilities, I have a need to keep the preheat the converter and the combustion furnace before the start, this will take about 48 hours. Summary of the sudden if you are willing Na temperature has been rising, and "power failure". Temperature of the converter is lowered, electricity is the place came also temperature increase start, repetition of ... down is also "a power outage!" And the temperature after a while.
The most frequent record, 35 times a power failure in one month. Indeed, the last became the mental state of "Kamidanomi".
Poor quality of "Made in local".
Steel pipe for boiler, to buy is called in the Japanese JIS and steel pipe which corresponds to the STB (Made in India) has been assembling a hot air dryer. Once I started to completion after water pressure test, and I still break in the longitudinal and "bread", "bread" from among you do not reach the default pressure! Apparently, it seemed to contain impurities in the drawing direction. Hurriedly and imported from Japan, I've not managed to meet the deadline to complete, it is ridiculous deficit.
Complaints came from customers.8. Acid circulation piping corrosion of
"Recently, the whole of the ventilation resistance increases, it does not flow as I think the gas, production volume is down."
A.
When you take a look, there is a large resistance to the shell side of the hot gas heat exchange of carbon steel (receive the gas from the converter first layer to the tube side).
At the time of periodic repair, if you saw it cut open the shell, has a whopping internal tightly packed with a thin film of iron oxide, flaky debris that it is broken.
Thin film, have overlapped in many layers round the outside of the tube, like "Baumkuchen". At a glance, it found an oxidation product tube has high-temperature oxidation.
Indeed, since the gas temperature from the first layer converter is about 600 ℃, carbon steel will be high-temperature oxidation. Such oxidation products are also not uncommon. However, it is amazing the amount. It does not stand still only construction after eight years.
We've heard your operations situation from the customer, here Toka he frequency of stop-start many, deliberate long-term stop five times a year by the production plan.
I found in it. On the surface of the long carbon steel exposed to high temperatures, of course oxidation products occurs. When you stop the plant decreases the temperature of the heat exchanger, the steel portion of the tube is then deflated, the portion of the oxide from the shrinkage rate is small steel, it will peel off from the surface. Usually, this "generation and cooling peeling" includes, but is should not only occur during the annual periodic maintenance, it is 5 times a year here, that is five times faster generation of standard amenities. In other words, the eight years of this equipment will mean that hits 40 years of ordinary equipment.
Eventually, it was replaced with a new heat exchanger that was all the tube SUS304. After that, our opinion, gas heat exchanger in a small equipment has changed the design criteria to be from the beginning made of SUS304.
And this customer, but there was one quarrel and around the expense of the heat exchanger update, it is omitted.
In new sulfuric acid plant, as the material of the circulation pipe of drying tower, absorption tower, it was specified the use of SUS316. Since the customer's is a company that has been involved in stainless steel production, and Toka I want to contribute to the consumption of stainless steel, even a little.9."Experts do not believe. "
However, operations start early, corrosion accident of the piping was frequent.
Elbow, cheese, such as downstream of the valve, it is remarkable to place, especially caused turbulence in the liquid.
Stainless steel, if the room temperature or less can be used in the long-term in SUS316, but does not recommend using it in place of more than 70 ℃ as the circulation pipe. For each impurity other factors in sulfuric acid, because there is otherwise with the case of long-lasting.
Actually this equipment, was in charge of the senior rather than me. SUS316 Once I heard the reason for the use, things and because it was specified customers as described above.
Most of the piping it was exchanged in Teflon lining pipe after all. From the customer, not issued gold because the responsibility of all us, and it has been told.
and "you, but, was the specified material of'm your" When you argue with, "When your company that would be a professional company? we are wrong, the duty should be there to point out that" the logic of the .
This is a fairly rough logic. Legal I do not know whether to but, but there is no not have such a feeling somehow.
"Failure both if unfortunate. If the expert, and useless compromise in technology surface"
It is a lesson that.
The tight is the words, but in particular young people, "" blind faith "absolutely useless" I want you to remember in the sense that.10.Impatient Na-Na get angry, give up
It is not directly related to sulfuric acid technology, but young, and there was that it tried to improve the facilities to get the SO3 by distillation of fuming sulfuric acid.
Because what kind of material was good or unknown, prepare a variety of test piece, put in the existing facilities, we have the corrosion test.
A result that was taken out after a certain period of time, violently corrosion as "higher material" at the time, towards the banal material is that the small amount of corrosion, it was what is contrary to "common sense" at the time.
I asked to visit us in the material manufacturer's Technical Director (Dr.), and sought an opinion on this result. This person, at the time was famous in Japan as a leading expert in the knowledge of metal material for sulfuric acid.
His view "this result is weird. I wonder how the test was bad. I would recommend this kind of Conditions if material XXXX" thing.
In his Suggested materials, where it drove by design and manufacture this equipment, the equipment in about two months corrosion can damage, it became the driving stop.
Again, where it was again the material test by installing a dedicated test equipment, it became almost the same result as the first test.
Even if there is fame of how much "guru", it was learned and it is important to believe the facts as facts.
Another is relatively recent, from I become officers.
In desulfurization of coke oven gas, facilities that my subordinates was in charge, all without put out the performance, now end up recreating some last line that was struggling. At the same time relationship that had received an order for more than one facility, it measures cost also became huge.
The reason for this was issued from the manufacturer of the oxidation apparatus of the circulating fluid for the "expected performance", and that in and is a "specialized manufacturer", "there are a large number of achievements", the person in charge was this even got to "swallow It was "thing.
However (it is that it was found later, but), because actual results up to now, even though height and circulating liquid composition and other conditions of the tower did different things fundamentally and this time, without having to pre-verification there it was that it had to blind faith to "study results of experts".
I will Yes "expert". However, he is not a God. It is to know knowledge is limited.
So I, for the customers when the technical advice "as above, but I think, whether or not adopted, please judge your company's responsibility" we have always said.
I have to work with quite long China local.11.There is no money from?
Initially, this word that was to ask from the direction of the local representative of the trading company. It seems to knowledge of business in China.
until the promised deadline to answer is no. Or it brings up again the conclusion of the previous meeting. Come was unabashedly a request not in the contract. How thought to stick to common sense out of the theory to the ...
And, here we are a few people, over there in the 10 times the number of people, you have been bubbling over unanimously.
In Shanghai Baoshan steel plant project, the construction period up to completion after receipt of order in the first place was 4 years 6 months. Was told to complain and "yeah! So if I do not I get a acceptance nearly five years even if the delivery?" From equipment manufacturers. From the instrument manufacturers "When you start the more, this time ordering our instrument was probably all specifications are revised, can not by the delivery of the same thing." It was also said to be.
And, impossible to achieve inspection criteria one after another.
"China-made equipment, the Well of you? Irassharu made in so strict standards, and import I want to," To tell you the irony and, undertone, in spear, and it while it says "I can not be in China."
Even if their own is possible, but I do it to the Japanese.
Because say that too insane, "such claims, I will not deviate from the common sense of the world" When chide with, "Ono teacher, Japan has a population of 130 million people. We Chinese are 1.3 billion people. Our people would be common sense of the world, "he said. No early, it does not come true.
Still, I, than the Japanese colleague who accompanied were, did not feel uncomfortable too strongly. Maybe, "to say only this, Chants I wish I wonder there is a reason" and, what because you have respect for the other party in its own way.
Even so, when you show off to juniors who are involved in business in China for more than experience in active duty, that of the "now is also true."
Will the "Chinese funny"? No, no, if you think it is now close to the position of third party, too homogeneous, be that those of Japanese society of "supposed to be seen not say" is heterogeneous in the world. In that sense, "more of us the world of common sense," it was Kyoben Shanghai technicians of words, might was right.
1990, we have come to the sulfuric acid plant commissioning of Panzhihua steel plant of the mountains of Sichuan.12.Black out (power outage)
We are making the sulfuric acid from the secondary raw sour gas at the time of desulfurization coke oven gas.
Our basic design and supply of some know-how equipment, in charge of commissioning the company detailed design of Germany, the Chinese side was the charge of the construction and supply equipment.
From the Chinese side "of the blower capacity There are three times the required amount, what? What should I do when" It was asked."Since the budget is tight," and Toka he has been looking for second-hand goods.
"From the blower outlet, please add the circulating gas piping back to the drying tower" I have been advised. Because too raise the gas temperature in many so recycling, it is dangerous if you do not cooling.
However flowmeter of the process gas because that is attached to the outlet of the drying tower, is also required flowmeter to recycling line. Than that "money to buy a flow meter is ...", I was raised doing in the service until the orifice of the design. Install the differential pressure gauge of visual, we were working to flow.
Chinese-made liquid level gauge attached to the pump tank of the absorption tower is also broken again and again. The wetted parts and Toka's are using a diaphragm of SUS316.
When you advice as "should I frog Hastelloy-C", as the "if made in China, you can buy five or more made in Japan one minute", "China is not made in", "please buy from Japan", to say The did not hear.
Then, in Shanghai of sulfuric acid equipment, orders the work to switch the thing was pyrite raw material sulfur raw materials, after four years of completion, was visited in aftercare at the request from the customer. It is that of 2000.
This seat was asked "because blower capacity is excessive you want to an inverter motor. Is it true, but say that it pays for itself in one year?". While I think that I wish not to change much, "Better yet, please had made the blower" You have advised, and whether you run ...
Eteshite in developing countries, say that "in the next few years will rise to profit" will not be welcome. Since we are replaced by more and more To leave the company, by the time you make a profit because his is not. Private companies and foreign is to same is true in China, because I want state-owned enterprises is also quite personnel changes, you will of similar. In other words, to raise the short-term performance, "to keep the current investment" it is's the best.
"Because there is no money" ... really, "I do not want to lower performance."
Of travelers from China of this year's Spring Festival, "爆買 physician", Is there in the place where it is.
As I wrote, even "work in developing countries", in the work in developing countries, infrastructure is different is very difficulty in whether or not been established. And do you say, but such infrastructure is what "still developing" So, "developing countries". Many and will be in direct problem the most, it is a power outage. The commissioning of Nigeria of sulfuric acid equipment, there was 35 times of power outage in January. It is preheated, barely power failure If you think the temperature went up. Barely been started, and ignited sulfur power failure If you think ... that began to be sulfuric acid. In addition, the troubled, it the prospect of recovery do not know. Because you repeat too, it has increasingly young I also become pessimistic. In Malaysia, construction initially at (1985) point, there was occasional power outage. However, in the current 30 years, it is that of the no it as good go at all To. Again, it's neat development. Young people, the electricity will be folded anywhere, anytime I think something in common. But, even in Japan, I have (which is before from now 60 years!) Childhood in, because the power failure was not uncommon, it was what had been equipped with a sure candles in the house. Come to think of it, the essentials candle in each house as well in Nigeria. Night, becomes a power outage in the middle of it is a mah-jong in Japanese to each other that had been dispatched in commissioning, and make a candle to the four corners of the table, we also can do as "Qi", "Pong" in the dark. When the electricity is restored see each other's face, it had become completely black with soot. It called Black out in English that of a power failure. Since the lighting of emergency is also small, and will meet in a power outage the night in developing countries, you really will experience the "jet-black darkness." Scary thing.
↧
Sulfuric Acid Safety
Sulfuric acid is strongly corrosive, it will severely damage the human body. Therefore, careful attention must be paid to the handling. In addition, injuries and respiratory by gas such as sulfuric acid facilities SO2 and SO3, there is also a danger of burns due to contact with high temperature equipment such as a furnace and converter. And these of prevention, we will discuss measures at the time of injury.
Image may be NSFW.
Clik here to view.
Sulfuric acid 1.Legal regulations
Clik here to view.
Gas 1.Danger and discovery
Image may be NSFW.
Clik here to view.

Fire Service Act: The sulfuric acid and oleum, but selfishness, there was strict regulations as a risk of the Fire Service Act, since 1990 I became a "non-hazardous material." However, sulfuric acid at a concentration of more than 60% has become necessary to report to the local fire department as a "firefighting inhibitor". For such specific filings, please contact your local fire department.2.Equipment Precautions
Poisonous and Deleterious Substances Control Law: Sulfuric acid in excess of 10 percent concentration will be crackdown target of this law as a deleterious substance. Manufacturing, which tries to import you must issue a registration application to the Minister of Health, Labour and Welfare through the prefectural governor. That tries to sell you registration application to the prefectural governor. Manufacture, storage, sale, there are regulations for transportation and disposal. Especially if are planning the construction of a sulfuric acid plant, it must be a satisfying design the regulation of manufacturing plants and storage plants.
Other than, Specific chemical substances such as disability prevention rule Petrochemical complex, etc. Disaster Prevention Law Let's keep in mind also to such.
Guests can prevent in the protective equipment, than the measures from happening accident, it is important prevention of accidents is the best. In this sense, drying tower, absorption tower, acid coolers, acid piping, devices that handle approximately sulfuric acid such as貯酸tank let's always prepared to be "corrosion to leave a hole." In the sense of prevention of accidents, 1) can be as long as 2 to adopt a highly corrosion-resistant material (such as Teflon)) In the case of metal material, regularly conduct the wall thickness measurement and internal inspection, 3 know the amount of corrosion) it is also happening leakage accident dikes so that it does not lead to human accident, protection wall, 4 it should be installed, such as double tube) acid facilities are separated as much as possible from such passage, but unavoidable time by a notice that it is a "danger" The ceiling to put 5) that travel on foot at risk, migratory floor is provided, it should be in so as not to climb directly to the ceiling board3.When working Note
Sulfuric acid is a strong acid, causing Gekijin of chemical injury on contact with the skin for dehydration action is strong. Therefore, at the time of handling of sulfuric acid, you must use the appropriate safety protective equipment.4.Safety equipment
Protection as the protection of the face shield ... eyes (in a normal protective glasses alone, is not allowed because there is a risk of sulfuric acid from entering from the gap) Protection of protection made of vinyl raincoat ... body of rubber gloves ... hand
During maintenance work to deal with sulfuric acid, in advance Always place immediately water hose beside, it is essential to work while flowing water at all times. When the sulfuric acid even took the body a little, as soon as possible, be washed with a large amount of water is required. In addition, during maintenance work on, such as tanks and pipes of sulfuric acid, there is a need to start working with even assuming "here still filled with sulfuric acid" even after internal to the sky. Often, the was a "going was in the sky" is, it may cause a slightly remaining serious accident for sulfuric acid.
In addition, containing a metal tanks and pipes of sulfuric acid may hydrogen gas produced by the corrosion are accumulated, This may cause an explosion. In the accident at I heard India, in an attempt to cut the lid with a gas burner and try to open the tank during the stop, hydrogen explosion will occur, there are cases that died four people. Hydrogen is lighter, so we accumulated in the top of the container, and from to open the upper part by a means that does not use the fire, let's habit is to begin working with the fire after you ventilate the interior by ventilation, if possible.
First of measures against burns of sulfuric acid, it is to "wash with water." In this sense, in the sulfuric acid plant, tower, acid cooler, such as acid piping, in the high places of the possibility of contact with the sulfuric acid, is required to be installed eye washer, the body washer. They are, as it is not to be obstructive to not come out of water in case of emergency, let's get in the habit of flowing water to determine the daily time. Also, in addition to these, let's provided here and there the nozzle out of the water and I open the manual valve. This is, at the same time as the meaning of safety, also required at the time of maintenance work to deal with sulfuric acid.5.Injury time measures
To measures of when the leakage of sulfuric acid occurs, let's standing dry sand and slaked lime. Especially sand, if caused to absorb the sulfuric acid prior to watering to the leaking sulfuric acid, is useful because you reduce the amount of sulfuric acid flowing into the drainage.
I've described above, first of measures against burns of sulfuric acid, is to "wash as soon as possible water". And to wash away the sulfuric acid from the skin, there is a sense that the cooling because it burns. Since sulfuric acid has a strong dehydrating action, and has remained even slightly, leaving a trail of serious burns to the skin and eventually concentrated. In this sense, it is essential that washing with water quickly even one minute one second. After sufficient washing with water, ask them to allowance and let diagnosis your doctor. If possible, let's examine a doctor with experience in medicine flaw in advance.Sulfur 1.Legal regulations
Fire Service Act: Sulfur is a hazardous material second class on the Fire Service Act. Since the specified quantity is 100kg, it must be carried out in the facility as defined in the Fire Service Act when the amount of sulfur and storage, transportation, and handling of more than this. Also, then you need to place the workers with a qualification of "hazardous materials handlers" (Class A or Class B second class) in the operation site, you must have posted as stipulated in other laws and regulations. For installation standards and other sulfur tank, Dangerous Goods Administration Study Group Author, Tokyo Fire Department supervision "Fast Facts illustration hazardous materials facility standards" It is the best. Amazon, you can net purchase at Kinokuniya other.2.Equipment Precautions
Sulfur, and ignition easy, occurs toxic SO2 gas by combustion. In addition, since it has been kept to 130 ~ 150 ℃ in steam in order to keep the molten state, let's attention to the burn.3.When working Note
Storage tank and pump, with regard to the structure of the pipe or the like, " new facilities -3 Please see others "sulfur tank" of ". Sulfur, allow it to easily solidified at room temperature, it is what it is less likely to result in a safety problem even if leaked. However, since it easily ignited, always Keep away from ignition source, it is important to try to extinguish quickly if you have any chance ignition. In the case of fire in the sulfur tank, you will first blowing steam. If still no signs of fire fighting, it will inject the water. Usually, since it has ignited in sulfur internal tank walls and ceiling, until the occurrence of SO2 comes to a complete stop and let's continue the fire fighting.
Molten sulfur to hydrogen sulfide odor, but usually it is not at the required level of gas mask. However, hydrogen sulfide, because the concentration is no longer felt to be high and the contrary sense of smell, is dangerous. In around the sulfur tank, let's implement the measurement of hydrogen sulfide concentration as necessary. This measurement, because the method is simple and quick by the detection tube, pump of the detector tube and measurement, let's standing in the field. As detector tube manufacturers Komyorikagakukogyo Co., Ltd. Co., Ltd. Gas Tech And so on.4.Injury time measures
Small amount of molten sulfur is also attached to the skin, abuses there is no other than the faint of skin to worry about cause burns, because it is dangerous to incur a large amount, wear protective goggles and gloves (leather is desirable) at a position other than the helmet , let's so as not to expose the skin. In addition, drained from the tank and piping was carried enough, under the attitude that "if either is filled to happens if had been" even after you disconnect, work to face and hands, and be careful on the position of the body Let's place.
Poisoning of hydrogen sulfide, because there is a danger of life, to move the injured person to a well-ventilated place, let's subjected to examination of as soon as the doctor can. In the case of burns, as well as the general of the burn, it is important to "as soon as possible cool". This is enough even in water.Image may be NSFW.
Clik here to view.

In the sulfuric acid plant, which flows through the containing harmful components gas facilities such as SO2 and SO3, and aspiration of these components by leakage accident and and respiratory failure, sometimes leading to severe cases suffocation death. If you have the generation of gas leak accident in equipment operation, but SO3 in the gas as long as it is a converter or later leakage source of discovery and it causes the white smoke of concentrated sulfuric acid reacts with H2O in the air it is easy, in front of the boiler and sulfur combustion furnace around than it is SO2 only, discovery of the leakage point is difficult. For this purpose, it is recommended that you standing ammonia water. When you soak the ammonia water in rags will close in the vicinity of the location where leakage is suspected, if there is a leakage, it causes the white smoke of sulfite Ammon by the reaction of SO2 and NH3 in the gas, it becomes possible to visually discover You. Ammonia water, put on poly jug, it would be good to try sprinkling in the vicinity of the location where leakage is suspected.2.Notes on work
Let's always work to wear a gas mask filled with adsorbent such as activated carbon. As a manufacturer, Ltd. Shigematsuseisakusho It is famous.3.Injury time measures
Move the injured person to a well-ventilated place, let's subjected to the treatment of the doctor as soon as possible. It can cause a pulmonary edema from the rare post-injury time passed, so some people over to respiratory It is also necessary that do not hit the work.
↧
450V 300KW generator rotor varnish treatment
↧